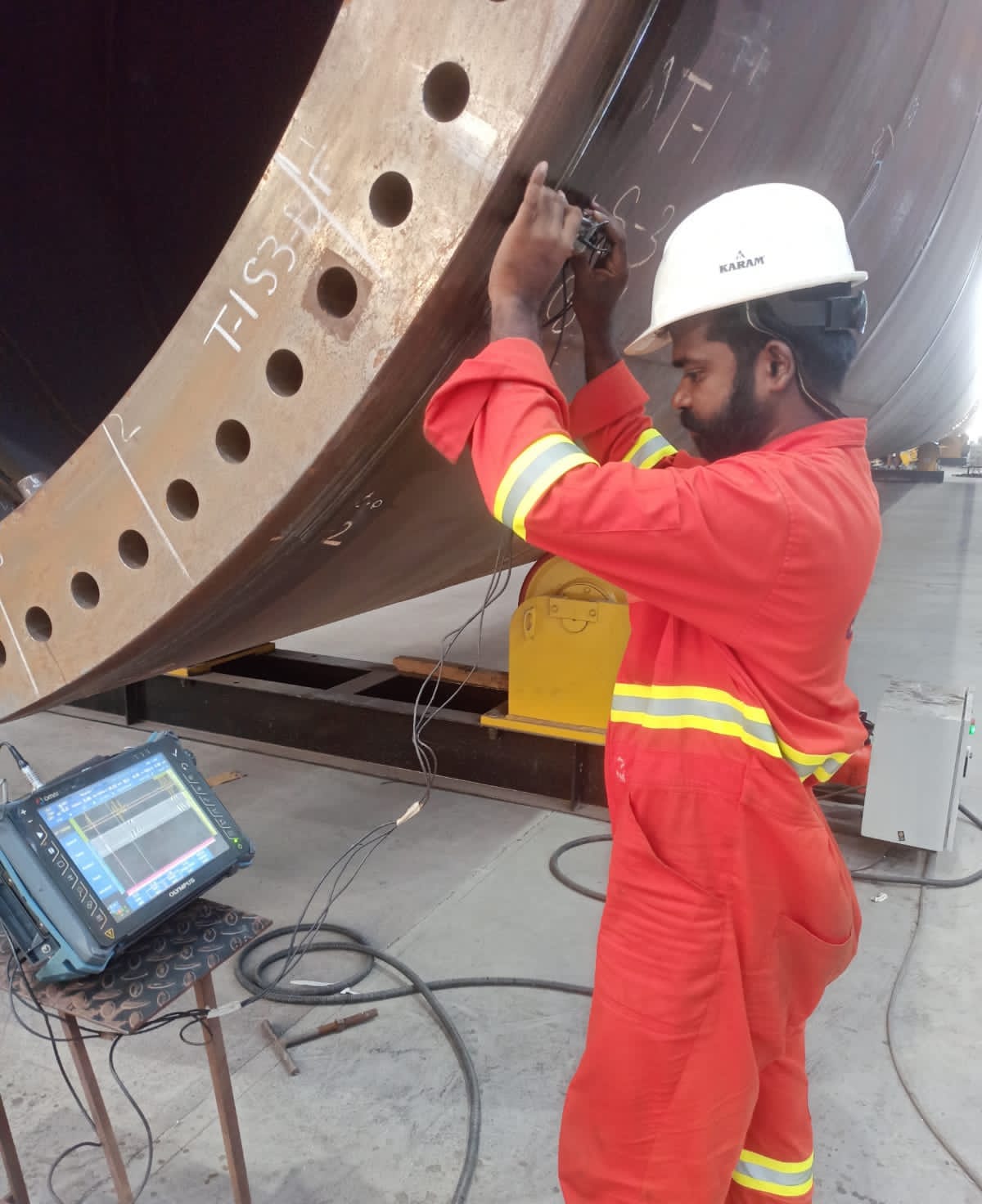
PHASED ARRAY ULTRASONIC TESTING (PAUT)
Phased Array Inspection (PAUT)
What is phased array inspection
Why it is called phased array and why it is used
Write a paragraph on applications of PAUT
Write a paragraph on benefits and advantages of PAUT
A current non-destructive testing (NDT) method used in evaluating welds, pipes, and other metallic structures is called phased array inspection (PAUT). It examines flaws or imperfections in a range of materials using cutting-edge ultrasound technology. Due to this technique’s great accuracy, speed, and dependability, it has gained popularity in the industrial sector and is a useful instrument for assuring safety, dependability, and efficiency in crucial industries including aerospace, oil and gas, and automotive. The arrangement of ultrasonic transducers in the probe known as a “phased array” is one in which each transducer is electronically regulated to emit and receive ultrasonic waves at a slightly different time. Thus, a concentrated and steerable ultrasonic beam is produced by phase-shifting the waves produced by each transducer so that they cancel out in certain directions and contribute constructively in others. Due to its advantages over conventional ultrasonic testing techniques, this technology is employed in non-destructive testing (NDT). A more thorough examination of the material is possible thanks to the ultrasonic beam’s capacity to be focused and guided, which enhances the ability to spot and measure flaws like fractures and gaps. Phased array technology also makes it possible to inspect intricate geometries and materials with various thicknesses and characteristics. Additionally, because it can produce thorough results with little surface preparation or disassembly of the investigated object, PAUT can be more economical than other procedures and offers faster inspection periods.
PAUT inspects materials for flaws or anomalies using ultrasonic waves, which are high-frequency sound waves. The method uses an array of small parts that are electronically controlled to focus and direct the ultrasound waves as well as a transducer to emit the ultrasound waves into the material. A more thorough and accurate inspection is possible thanks to the phased array transducer’s ability to produce several ultrasonic beams with variable amplitude and direction. Inspectors can find and pinpoint any flaws or problems using the system’s ability to provide detailed photographs of the material’s inside.
There are a number of reasons why PAUT is preferred to conventional ultrasonic testing techniques, including
Higher resolution and more effective defect identification are possible with the phased array probe’s concentrated and steerable ultrasonic beams. It makes it possible for inspectors to precisely find and measure imperfections like fractures, cavities, and inclusions.
Since PAUT can inspect greater areas with fewer passes than conventional methods, inspection times can be shortened.
Since it can produce comprehensive data with little surface preparation or disassembly of the inspected object, PAUT may be more cost-effective than other approaches. When evaluating huge and complicated constructions, in particular, this can save time and money.
Due to its adaptability, PAUT can examine a wide range of materials, forms, and thicknesses. It is frequently used for examining crucial parts like welds, pressure vessels, and pipelines in sectors including aerospace, automotive, and oil & gas.
Many industries utilize phased array ultrasonic testing (PAUT) to evaluate metallic constructions like welds, pipes, pressure vessels, and turbines. Wings, engine blades, and landing gear are among the aircraft parts that PAUT is used to examine in the aerospace sector. Internal flaws including fractures, corrosion, and delamination that might lead to failure and jeopardize safety can be found with PAUT. PAUT is utilised in the automobile sector to inspect vital parts such engine blocks, crankshafts, and connecting rods. By detecting corrosion and other types of material degradation, PAUT enables prompt maintenance and repair. To assure the structural integrity of composite materials used in automotive and aerospace applications, PAUT may inspect them. To find any flaws or vulnerabilities, PAUT can evaluate structural elements such as bridges and buildings. In the oil and gas sector, PAUT is also used to inspect refineries, tanks, and pipelines. The method is important for identifying corrosion, cracking, and weld faults in these buildings, which can result in leaks and environmental risks. Additionally, PAUT is used in production to check the quality of produced components to make sure they adhere to strict design specifications. Compared to conventional inspection methods, PAUT has a number of benefits, including:
More rapid inspections are possible thanks to PAUT’s improved speed at scanning huge regions.
The phased array transducer may produce numerous ultrasonic wave beams, enabling a more thorough and accurate inspection.
PAUT can be carried out by a smaller workforce, which lowers labour costs and boosts productivity.
PAUT is a non-destructive method that doesn’t call for material destruction or damage, making it a safer and more ecologically friendly choice.
As a result of its greater resolution, quicker inspection times, cost-effectiveness, and versatility in inspecting complicated geometries and materials, PAUT is preferable to conventional ultrasonic testing techniques. PAUT is used in a variety of sectors and offers a dependable and effective non-destructive testing method for identifying internal flaws and assuring structural integrity. It is a popular option for checking crucial components and materials because of its capacity to deliver quick and precise inspection findings. Even though PAUT has various drawbacks and difficulties, it is nevertheless a vital and developing technology that is assisting in enhancing the performance and safety of industrial processes and goods.
Ideal for non-invasive material examinations, for finding flaws.
For More Information Contact Our Expert Team: support@solutionss.org