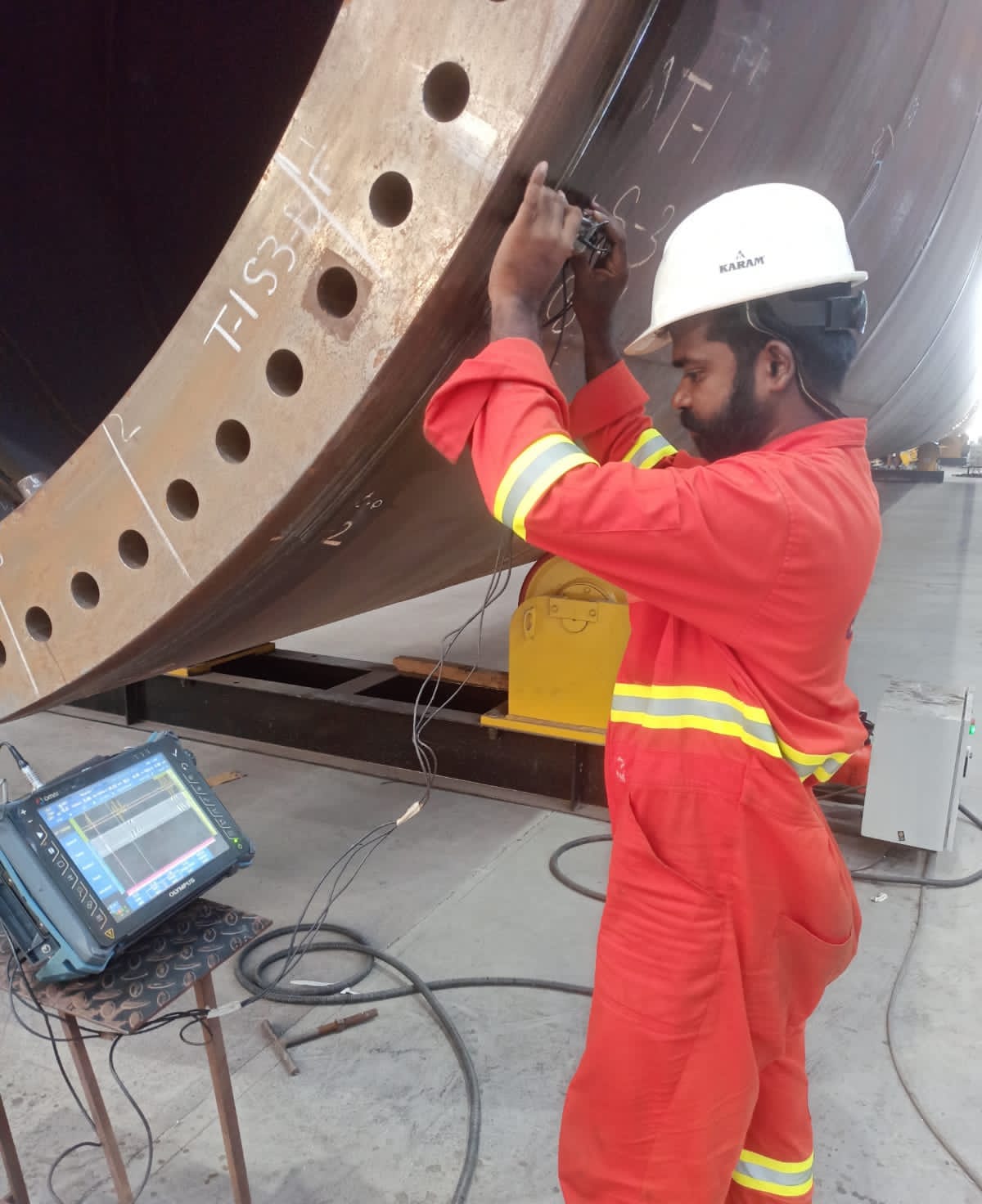
Phased Array Inspection (PAUT)
Phased Array Inspection (PAUT)
Introduction:
Non-Destructive Testing (NDT) plays a crucial role in ensuring the safety, reliability, and quality of industrial equipment and structures. Among the various NDT techniques, Phased Array Ultrasonic Testing (PAUT) has emerged as a highly efficient and advanced method for inspecting materials and detecting flaws. This article explores the significance of PAUT in the NDT industry and highlights NDT and PWHT Solutions as a leading company that excels in delivering PAUT services. Furthermore, we will delve into what sets this company apart from its competitors and makes it the preferred choice for clients seeking high-quality inspection services.
Understanding Phased Array Inspection (PAUT):
Phased Array Ultrasonic Testing (PAUT) employs advanced ultrasonic technology to inspect materials, detect discontinuities, and assess the integrity of structures. This technique utilizes multiple ultrasonic elements and phased array probes that can emit and receive ultrasonic waves at various angles and focal distances. By manipulating the timing and amplitude of these waves, PAUT enables comprehensive inspections of complex geometries and provides accurate flaw detection, sizing, and imaging capabilities. Its versatility, speed, and precision make PAUT a preferred choice in various industries such as aerospace, oil and gas, manufacturing, and infrastructure.
NDT and PWHT Solutions: Delivering Unparalleled PAUT Services:
NDT and PWHT Solutions have established themselves as a prominent name in the NDT industry, renowned for their expertise in PAUT. With a team of highly skilled and certified professionals, the company offers comprehensive PAUT inspection services, catering to the diverse needs of their clients. NDT and PWHT Solutions pride themselves on their commitment to excellence, providing accurate and reliable inspection results that adhere to the highest industry standards.
Unmatched Technical Proficiency:
NDT and PWHT Solutions boast a team of extensively trained and experienced technicians who possess a deep understanding of PAUT principles and applications. Their expertise allows them to develop customized inspection strategies tailored to each client’s unique requirements. By employing state-of-the-art equipment and cutting-edge techniques, they ensure that every inspection is conducted with precision and efficiency
Advanced Technology and Equipment:
To maintain their competitive edge, NDT and PWHT Solutions continuously invest in the latest technology and equipment. They utilize advanced phased array systems and high-resolution scanners, which enable faster data acquisition, improved imaging quality, and enhanced defect characterization. By staying at the forefront of technological advancements, the company ensures that their clients benefit from the most accurate and reliable inspection results available.
Commitment to Quality and Safety:
NDT and PWHT Solutions prioritize quality and safety in every aspect of their operations. They adhere to stringent quality control procedures, ensuring that their inspection processes meet or exceed industry standards and regulations. The company’s commitment to safety extends to their technicians who undergo regular training and certifications, ensuring their competence and compliance with industry best practices.
Tailored Solutions and Flexibility:
Understanding that every client and project is unique, NDT and PWHT Solutions provide tailored inspection solutions to address specific requirements. They collaborate closely with clients, understanding their objectives and challenges, and then design comprehensive inspection plans that maximize efficiency and accuracy. The company’s flexibility allows them to adapt to varying project scopes, timelines, and budgets while maintaining the highest quality standards.
Comprehensive Reporting and Data Analysis:
NDT and PWHT Solutions go beyond conducting inspections; they deliver comprehensive reports and data analysis to their clients. The company employs advanced software and algorithms to analyze inspection data, generating detailed reports with precise flaw sizing, imaging, and classification. Their reports are presented in a clear and understandable format, enabling clients to make informed decisions regarding asset integrity and maintenance strategies.
Conclusion:
Phased Array Ultrasonic Testing (PAUT) has revolutionized the NDT industry, offering unmatched inspection capabilities for ensuring the integrity of critical assets. In this realm, NDT and PWHT Solutions stand out as a leading provider of PAUT services, thanks to their technical expertise, advanced technology, commitment to quality and safety, tailored solutions, and comprehensive reporting. By choosing NDT and PWHT Solutions, clients can be confident in receiving the highest standard of PAUT inspections, enabling them to make informed decisions regarding asset maintenance, safety, and reliability.
Phased Array Ultrasonic Testing (PAUT) is a powerful and versatile non-destructive testing (NDT) technique widely used in various industries. It offers several benefits that make it highly advantageous in the NDT industry. Here are some of the key benefits of PAUT:
Improved Inspection Speed: PAUT allows for rapid inspection as it utilizes multiple ultrasonic beams simultaneously. By electronically steering and focusing the ultrasonic beam, PAUT can cover a larger area in a single scan, reducing inspection time compared to conventional single-element probes.
Greater Inspection Coverage: PAUT employs an array of small transducer elements that can be individually controlled. This enables the inspection of complex geometries and curved surfaces with enhanced coverage. It provides better detection capabilities for flaws in areas that are difficult to access or inspect using other methods.
Enhanced Defect Detection: PAUT offers high-resolution imaging and superior flaw detection capabilities. The ability to adjust focal depth and beam steering allows for precise targeting of specific areas of interest. By controlling the timing and amplitude of individual elements, PAUT can optimize flaw detection sensitivity and improve defect characterization.
Real-time Imaging: PAUT produces real-time cross-sectional images known as sector scans or B-scans. These images provide immediate feedback to the operator, enabling quick interpretation and decision-making during the inspection process. Real-time imaging facilitates faster defect identification, localization, and evaluation.
3D Inspection Capabilities: PAUT can be combined with mechanical scanners or encoded robotic systems to perform automated 3D scanning. This allows for comprehensive volumetric inspections of complex components, such as welds, turbine blades, or composite structures. The ability to capture and analyze data in three dimensions enhances defect detection accuracy and provides valuable information for integrity assessments.
Increased Probability of Detection (POD): The advanced beam manipulation capabilities of PAUT result in improved probability of detecting and characterizing flaws accurately. By optimizing the ultrasonic beam direction, focusing, and sensitivity settings, PAUT helps ensure that even small or subtle defects are not missed during inspections.
Reduced Couplant Usage: PAUT systems can utilize water or dry coupling methods, reducing or eliminating the need for large amounts of couplant (e.g., gel or oil). This feature makes PAUT more environmentally friendly and reduces the cleaning and post-inspection preparation time.
Data Archiving and Analysis: PAUT systems often include advanced software for data acquisition, storage, and analysis. This allows for efficient data management, report generation, and integration with other inspection processes or quality control systems.
In summary, PAUT offers numerous benefits in the NDT industry, including faster inspections, improved defect detection, advanced imaging capabilities, 3D scanning, and efficient data management. These advantages make PAUT a valuable tool for ensuring the integrity and quality of critical components in various industries, such as aerospace, oil and gas, power generation, and manufacturing.
wide variety of inspection and measurement applications, and they can be used for any job done by conventional ultrasonics.
For More Information Contact Our Expert Team: support@solutionss.org