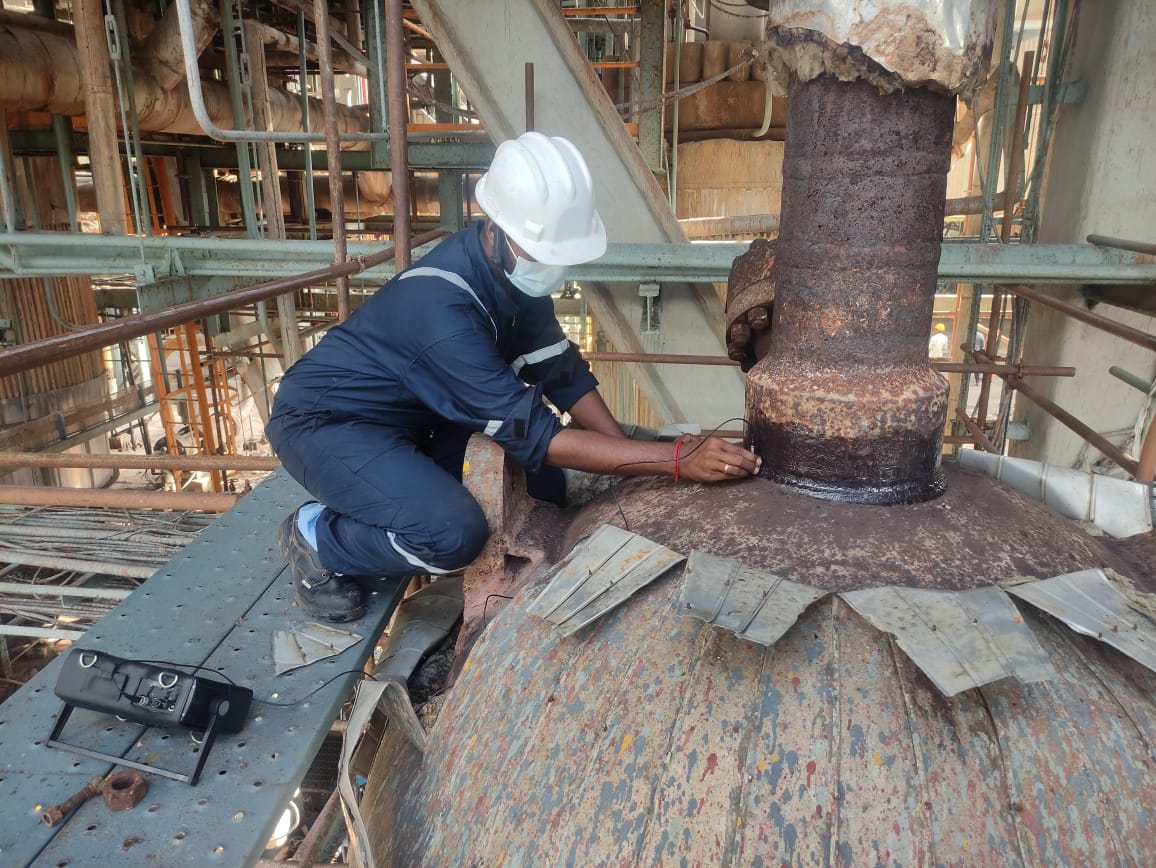
HIGH TEMPERATURE UT THICKNESS GAUGING
High Temperature Ultrasonic Thickness Gauging (UT)
A non-destructive testing (NDT) method used to gauge a material’s thickness even at high temperatures is high-temperature ultrasonic thickness gauging. This technique is particularly helpful for businesses that use high-temperature machinery like boilers, furnaces, and pipes. Utilizing ultrasonic waves, the ultrasonic thickness gauging method is used to gauge the thickness of materials, often metals, polymers, or composites. It is the best approach for testing materials that are currently in use, like pipelines or pressure vessels, because it is non-invasive and causes no harm to the substance being examined. This method is also incredibly accurate, producing exact measurements even on intricate surfaces or shapes. It helps to assure the quality and safety of materials and products and is beneficial in a variety of industries and applications.
High-frequency sound waves are transmitted through the material using the ultrasonic thickness measuring technique, and they are subsequently reflected back to the gauge. The gauge calculates how long it takes for sound waves to leave the source and return to it after passing through the material. The gauge determines the thickness of the material based on this time measurement. Special probes are utilized for high-temperature ultrasonic thickness gauging. These probes are built of materials that are compatible with the temperature and the material being tested and are designed to resist high temperatures, often up to 600°C (1112°F) or more. For instance, a dual element probe with a high-temperature wedge constructed of high-temperature plastic and high-temperature couplant is used for testing carbon steel at high temperatures. The non-destructive nature of high-temperature ultrasonic thickness gauging is one of its key benefits. This indicates that, unlike other testing procedures, the tested equipment does not need to be taken out of operation or cut open. This technique is also quite accurate and can measure thickness precisely on materials with intricate surfaces or geometries.
In many different areas, including manufacturing, construction, and aerospace, ultrasonic thickness measuring is a helpful tool. It is employed in production to guarantee the uniformity of material thickness and to look for any flaws or defects that can impair the final product’s quality. It is used in construction to check the structural components’ thickness and make sure they adhere to design criteria. In the aerospace industry, it is used to keep track of the thickness of aircraft parts like wings and fuselages as well as to look for any corrosion or other damage that would jeopardize the aircraft’s safety. This method offers exact measurements of material thickness, enabling prompt equipment replacements or repairs before breakdown occurs.
High-temperature ultrasonic thickness gauging benefits the industry in the following ways:
By using high-temperature ultrasonic thickness gauging, it is possible to identify material thinning or corrosion before it poses a risk to safety or leads to equipment failure. Industries can prevent expensive downtime and repairs by identifying sections that need maintenance or replacement.
Increased equipment reliability can be attained through the routine use of high-temperature ultrasonic thickness gauging, which can assist industries in locating worn-out parts. This lessens the possibility of unplanned shutdowns or equipment breakdowns and increases equipment reliability.
High-temperature ultrasonic thickness gauging is a non-destructive testing method that may be carried out while machinery is still in use, obviating the need for shutdowns or downtime. This decreases production losses and equipment downtime, saving businesses time and money.
Businesses can enhance safety by determining which parts of their equipment or materials require maintenance or replacement. This will help them make sure that everything is operating properly and within safe limits.
Industries benefit from high-temperature ultrasonic thickness gauging by enhancing equipment dependability, preventing equipment failure, saving time and money, and enhancing safety. It is a useful tool for enterprises that need to guarantee the security and effectiveness of their operations while using equipment and materials that work at high temperatures.
The application of high-temperature ultrasonic thickness gauging is considerable, particularly in high-temperature operating sectors. Even at high temperatures, often up to 600°C (1112°F), this non-destructive testing (NDT) technology enables reliable and precise measurements of the thickness of materials. Petrochemical, power generating, and metallurgical industries frequently employ high-temperature ultrasonic thickness gauging. It is employed in the petrochemical industry to gauge the thickness of tanks, pipes, and other oil and gas storage and transportation-related machinery. It is used in power generating to gauge the thickness of turbine blades, boilers, and other parts involved in energy production. It is used in metallurgy to gauge the thickness of furnace linings and other high-temperature metalworking materials. This method enables accurate readings without the need for the equipment to be stopped or cooled down, which can be time-consuming and expensive in industries that run at high temperatures. Locating potential areas of corrosion or other damage, it can also help to prevent equipment failure by enabling prompt replacement or repair. This method can help avoid expensive downtime and maintenance while ensuring the efficiency and safety of machinery and materials that operate at high temperatures.
An effective NDT method for high-temperature industry is high-temperature ultrasonic thickness gauging. It makes it possible to measure material thickness accurately and without causing damage, and it aids in ensuring the reliable operation of high-temperature machinery.
For More Information Contact Our Expert Team: support@solutionss.org