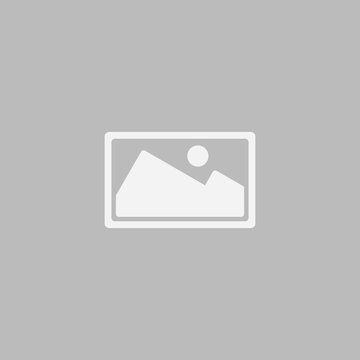
The Role of NDT in Oil & Gas Industry Inspections
Introduction
The oil and gas industry operates in some of the most challenging and hazardous environments, where the integrity of equipment and infrastructure is critical to both safety and operational efficiency. The risk of failure due to material degradation, corrosion, cracks, or fatigue can lead to disastrous consequences, including loss of life, environmental damage, and substantial economic loss.
To prevent such failures, Non-Destructive Testing (NDT) has become a crucial part of inspection, maintenance, and quality assurance processes across the oil and gas sector. NDT provides an effective, cost-efficient, and safe means of inspecting critical components without compromising their functionality or operational readiness.
This article delves into the role of NDT in the oil and gas industry, exploring various testing methods, their applications, and the importance of these technologies in ensuring safe, reliable operations.
The Importance of NDT in the Oil & Gas Industry
The oil and gas industry is particularly vulnerable to the impact of material degradation. The extreme environments in which these facilities operate – from high-pressure pipelines deep under the ocean to equipment exposed to corrosive gases and chemicals – create a constant threat to the integrity of materials used. Some of the key challenges include:
Corrosion: A common issue in oil and gas infrastructure, especially in pipelines, tanks, and offshore platforms, where constant exposure to saltwater, chemicals, and moisture accelerates corrosion.
Fatigue Cracks: Equipment that undergoes repeated loading cycles, such as pipelines and pressure vessels, is prone to fatigue cracks that can grow over time, leading to catastrophic failures if undetected.
Weld Integrity: Welds in pipelines, pressure vessels, and offshore platforms are subject to high stress and thermal cycling, making them susceptible to cracks and voids that can compromise structural integrity.
Cement and Bonding Failures: In wellbore operations, cement and bonding failures can lead to a loss of integrity in casing and well barriers.
In addition to addressing these challenges, NDT helps ensure compliance with industry regulations, extend the operational life of equipment, and improve safety standards.
NDT Methods in Oil & Gas Industry Inspections
Various NDT techniques are employed in the oil and gas sector to detect defects, corrosion, and other issues in materials and structures. These techniques help identify problems early, minimizing the need for costly repairs and reducing the risk of failure.
1. Ultrasonic Testing (UT)
Ultrasonic Testing (UT) is widely used in the oil and gas industry for its ability to detect both surface and subsurface defects. High-frequency sound waves are sent through materials, and the resulting echoes are analyzed to detect anomalies such as cracks, voids, or inclusions. In the oil and gas industry, UT is used to:
Inspect pipelines for corrosion, cracks, and wall thinning, particularly in areas prone to erosion and corrosion.
Evaluate welds in pressure vessels, tanks, and piping systems for defects like porosity, cracks, and lack of fusion.
Measure material thickness in critical components such as offshore platform legs and pipelines to assess corrosion or erosion.
Advanced techniques such as Phased Array Ultrasonic Testing (PAUT) provide more detailed, high-resolution imaging, making it easier to detect smaller or more complex defects.
2. Magnetic Particle Testing (MPT)
Magnetic Particle Testing (MPT) is a powerful method for detecting surface and near-surface defects in ferromagnetic materials. It is especially useful in the oil and gas industry for inspecting critical components such as pipelines, storage tanks, and pressure vessels. In MPT, a magnetic field is applied to the component, and fine magnetic particles are used to reveal defects. MPT is used for:
Inspecting welds and joints for surface cracks, porosity, or fatigue.
Evaluating pressure vessels and tanks for signs of cracking or corrosion.
Assessing fasteners, valve bodies, and other metallic components for surface-breaking defects.
MPT is particularly effective in detecting cracks in welds, which are common in oil and gas infrastructure subjected to thermal cycling and high stress.
3. Eddy Current Testing (ECT)
Eddy Current Testing (ECT) is used for detecting surface and subsurface cracks and defects in conductive materials. The method involves inducing a magnetic field into the material, creating electrical currents (eddy currents) that interact with defects. In the oil and gas industry, ECT is employed for:
Inspections of pipelines, heat exchangers, and pressure vessels for cracks, corrosion, and wear.
Detecting material thinning and other issues in highly stressed components such as compressor blades and turbine parts.
Evaluating welded joints for porosity, cracking, and inclusions.
ECT is particularly beneficial for inspecting thin-walled or hard-to-reach parts, offering a quick and non-invasive inspection method.
4. Radiographic Testing (RT)
Radiographic Testing (RT) involves the use of X-rays or gamma rays to examine the internal structure of components. RT provides high-resolution images that reveal internal defects such as cracks, voids, or inclusions. In the oil and gas industry, RT is used to:
Inspect welds in pipelines, pressure vessels, and tanks for internal defects that are not visible on the surface.
Evaluate casings and wellbores for structural integrity, ensuring there are no issues with bonding or cementing.
Detect internal corrosion in structures like offshore platforms and underwater pipelines.
Digital radiography (DR) has become increasingly popular due to its ability to produce faster, clearer images and reduce radiation exposure.
5. Dye Penetrant Testing (DPT)
Dye Penetrant Testing (DPT) is a simple yet effective method for detecting surface-breaking defects in non-porous materials. A dye is applied to the surface, and after a brief period, excess dye is removed, leaving any surface defects visible under ultraviolet light. In the oil and gas industry, DPT is often used to:
Inspect welds and pressure vessels for surface cracks, pits, and other defects.
Evaluate components exposed to harsh environments for signs of damage or corrosion.
Detect leaks in tanks and pipelines, which are critical to maintaining environmental and operational safety.
DPT is particularly useful for quickly checking areas that are prone to surface damage and is often used in combination with other methods for more comprehensive assessments.
6. Visual Testing (VT)
Visual Testing (VT) is one of the simplest NDT methods but remains indispensable in the oil and gas industry. It involves a visual examination of the equipment and components to detect visible signs of wear, corrosion, or damage. In the oil and gas industry, VT is used for:
Routine inspections of tanks, pipes, and offshore platforms for signs of external damage, corrosion, or leaks.
Assessing equipment for Foreign Object Damage (FOD), which can occur during manufacturing, maintenance, or transport.
Monitoring for structural degradation in critical components like pipelines, valves, and tanks.
VT can be performed both on-site and remotely with the use of drones or cameras, making it a versatile and cost-effective solution.
Benefits of NDT in the Oil & Gas Industry
Enhanced Safety: NDT ensures that critical equipment is thoroughly inspected for defects that could lead to catastrophic failures, thus safeguarding personnel and the environment.
Cost-Effectiveness: By detecting defects early, NDT helps prevent costly repairs or replacements, saving money in the long term.
Regulatory Compliance: NDT ensures compliance with industry regulations and standards such as those set by the American Petroleum Institute (API), the International Organization for Standardization (ISO), and other relevant bodies.
Increased Asset Life: Regular NDT inspections help extend the operational life of oil and gas infrastructure, reducing the need for premature replacements.
Improved Operational Efficiency: By minimizing downtime and preventing unplanned maintenance, NDT contributes to the smooth and efficient running of oil and gas operations.
Conclusion
Non-Destructive Testing is indispensable in the oil and gas industry, offering a range of benefits from improving safety to extending the lifespan of critical infrastructure. The application of advanced NDT techniques such as Ultrasonic Testing (UT), Eddy Current Testing (ECT), Radiographic Testing (RT), and Magnetic Particle Testing (MPT) ensures that oil and gas companies can maintain the integrity of their assets while minimizing risks and ensuring regulatory compliance.
At NDT AND PWHT SOLUTIONS PVT LTD (India), we provide cutting-edge NDT solutions that help safeguard oil and gas operations across the globe. Our expert team is equipped with the latest technologies to deliver accurate, reliable, and efficient inspection services, ensuring the safety and longevity of critical infrastructure in the oil and gas sector.
By incorporating NDT into regular inspection routines, oil and gas companies can reduce risk, enhance safety, and improve operational efficiency, ultimately contributing to the sustainable growth of the industry.