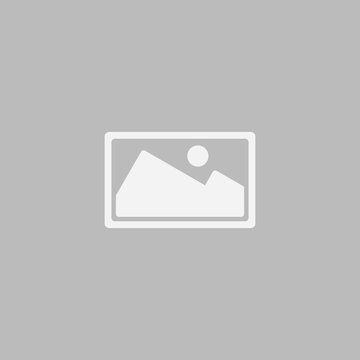
The Role of NDT in Offshore and Onshore Oil and Gas Inspections
Introduction
The oil and gas industry is one of the most critical sectors, with operations spanning both offshore and onshore sites. From exploration to production, the integrity of equipment and structures is paramount. Oil and gas facilities, including offshore rigs, pipelines, and refineries, operate in some of the harshest environments on earth. These conditions can cause equipment to degrade, leading to operational risks, safety hazards, and environmental threats.
Non-Destructive Testing (NDT) is an essential part of maintaining the safety, reliability, and efficiency of oil and gas assets. By using NDT techniques, companies can detect hidden defects and prevent catastrophic failures. This article discusses the role of NDT in offshore and onshore oil and gas inspections and highlights key inspection methods used to ensure asset integrity.
The Importance of NDT in Oil and Gas Industry
The oil and gas industry faces several challenges in maintaining the integrity of its equipment, including:
Corrosion: The presence of harsh chemicals, high pressures, and saltwater exposure accelerates corrosion of metal components.
Fatigue: Repeated cycles of loading and unloading, as well as environmental stressors, lead to material fatigue, especially in pipelines and offshore structures.
Erosion: The movement of sand, water, and other materials can erode the surfaces of pipelines and other equipment.
Weld and Joint Failures: Improper welding or joint fatigue can cause failures in critical areas of oil rigs, pipelines, and refineries.
Regular inspection and maintenance of these assets are essential to minimize risks, ensure operational efficiency, and avoid costly repairs or replacements. NDT techniques are non-invasive and can detect internal defects, allowing for early intervention and cost-effective maintenance.
NDT Methods Used in Oil and Gas Inspections
1. Ultrasonic Testing (UT)
Ultrasonic Testing (UT) is one of the most widely used methods in the oil and gas industry. It involves sending high-frequency sound waves through materials and measuring the time it takes for the waves to reflect back from defects or the far side of the material. UT is used to:
Inspect pipeline integrity: UT can detect internal corrosion, cracks, and material thinning in pipelines that are transporting oil, gas, or chemicals.
Assess welds: UT is used to inspect welds in offshore platforms, refineries, and other critical components for defects such as porosity, cracking, or inclusions.
Measure wall thickness: UT is essential for measuring the remaining wall thickness of metal pipes and structures, identifying areas vulnerable to corrosion or erosion.
With advanced techniques like Phased Array Ultrasonic Testing (PAUT) and Time-of-Flight Diffraction (TOFD), UT can provide high-resolution images and accurate defect characterization, ensuring comprehensive asset assessments.
2. Magnetic Particle Testing (MPT)
Magnetic Particle Testing (MPT) is commonly used to detect surface and near-surface defects in ferromagnetic materials. This method is useful for:
Inspecting pipelines and tanks: MPT is used to detect cracks, weld defects, and fatigue in steel pipelines and tanks.
Examining critical structures: Offshore oil rigs and platform legs can be inspected for fatigue and cracking using MPT.
Assessing welds: MPT is widely applied to detect surface-breaking defects in welded joints, particularly in high-stress areas.
MPT is a rapid, cost-effective way to inspect the surface of components, and it can be performed in-field during routine maintenance.
3. Eddy Current Testing (ECT)
Eddy Current Testing (ECT) is a versatile method used for detecting surface and subsurface defects in conductive materials. ECT is often employed in:
Inspecting pipelines and heat exchangers: ECT can detect surface cracks, corrosion, and material degradation in critical pipeline sections and heat exchangers.
Assessing tubing and casings: In offshore oil and gas operations, ECT is used to inspect the integrity of tubing and casing in wells for signs of corrosion or wear.
Monitoring fatigue and erosion: ECT is effective in monitoring materials for fatigue cracking or erosion, particularly in high-stress environments.
ECT is ideal for non-ferrous materials such as aluminum and copper alloys and can be used in conjunction with other methods for comprehensive inspections.
4. Radiographic Testing (RT)
Radiographic Testing (RT) uses X-rays or gamma rays to inspect the internal structure of materials. RT is valuable for:
Weld inspections: RT is commonly used for inspecting welds in pipelines, pressure vessels, and offshore platforms for defects that cannot be detected by surface methods.
Examining critical components: RT is used to inspect the internal integrity of components such as pressure vessels, piping, and risers.
Assessing material degradation: RT can identify internal corrosion, voids, or inclusions in materials, providing insight into the overall condition of the equipment.
Digital Radiography (DR) enhances RT capabilities by providing high-resolution images and faster processing times, making it ideal for inspecting large areas and complex components.
5. Visual Testing (VT)
Visual Testing (VT) is the most straightforward and commonly used NDT method. VT is essential for:
Routine inspections: VT is used for preliminary inspections to identify visible signs of corrosion, wear, or damage in pipelines, tanks, and other structures.
Monitoring conditions: VT is used to check the condition of protective coatings, seals, and other exterior elements to ensure they remain intact.
Ensuring maintenance standards: VT helps ensure that components are clean and free from obvious defects before more advanced testing methods are employed.
While VT does not detect internal defects, it is a critical part of the overall inspection process and is often combined with other NDT techniques for comprehensive assessments.
6. Dye Penetrant Testing (DPT)
Dye Penetrant Testing (DPT) is used to detect surface-breaking defects in non-porous materials. DPT is commonly used for:
Inspecting welds and joints: DPT is applied to detect surface cracks or other defects in welded components, valves, and pipe joints.
Identifying corrosion pits: DPT is useful for detecting small surface pits caused by localized corrosion.
Examining turbine blades and other high-stress components: DPT is used to inspect critical components in turbines, compressors, and other machinery for surface defects.
DPT is a cost-effective, reliable method for detecting surface flaws and can be easily implemented in the field.
Benefits of NDT in Oil and Gas Industry
Enhanced Safety: Regular NDT inspections help identify defects before they lead to catastrophic failures, ensuring the safety of workers, the environment, and nearby communities.
Cost Savings: By detecting defects early, NDT can prevent expensive repairs and replacements, reducing downtime and extending the service life of equipment.
Regulatory Compliance: NDT ensures that oil and gas operators comply with industry regulations and safety standards, such as those set by the American Petroleum Institute (API), the International Maritime Organization (IMO), and other regulatory bodies.
Operational Efficiency: NDT techniques allow for continuous monitoring of equipment condition, improving asset management and reducing operational risks.
Environmental Protection: By preventing equipment failures that could lead to spills, leaks, or other environmental hazards, NDT plays a key role in protecting natural resources and wildlife.
Conclusion
Non-Destructive Testing is a vital part of the oil and gas industry’s maintenance and safety strategy. Through techniques such as Ultrasonic Testing (UT), Magnetic Particle Testing (MPT), Eddy Current Testing (ECT), Radiographic Testing (RT), Visual Testing (VT), and Dye Penetrant Testing (DPT), operators can monitor the integrity of pipelines, rigs, and refineries, ensuring early detection of defects and reducing the risk of catastrophic failures.
At NDT AND PWHT SOLUTIONS PVT LTD (India), we offer cutting-edge NDT services tailored to the specific needs of the oil and gas industry. Our team of skilled inspectors uses advanced technologies to provide accurate, efficient, and reliable inspection solutions, helping our clients maintain operational safety, compliance, and environmental responsibility.
By incorporating NDT into routine inspection practices, oil and gas companies can achieve long-term asset reliability, minimize downtime, and protect both their assets and the environment.