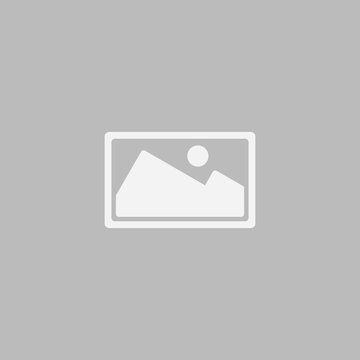
The Role of NDT in Marine & Offshore Inspections
Introduction
The marine and offshore industries are some of the most demanding sectors when it comes to maintaining the structural integrity and safety of vessels, platforms, and subsea systems. Harsh environments, including exposure to saltwater, extreme weather conditions, and constant wear and tear, contribute to a heightened risk of corrosion, fatigue, and mechanical failure. In these industries, it is critical to ensure the reliability of components, as even minor defects can lead to catastrophic consequences, including oil spills, loss of life, and significant financial losses.
Non-Destructive Testing (NDT) plays an essential role in ensuring the integrity of marine and offshore infrastructure. By providing an accurate, efficient, and safe means of detecting material defects without causing damage, NDT helps extend the lifespan of equipment, maintain safety standards, and reduce operational risks.
This article explores the significance of NDT in the marine and offshore industries, outlining the various techniques used and their applications in maintaining safe, efficient operations.
The Importance of NDT in Marine & Offshore Inspections
Marine and offshore operations often deal with extreme conditions that accelerate material degradation. The continuous exposure to saltwater, high pressure, and fluctuating temperatures contributes to the risk of corrosion, cracks, and other forms of damage that may compromise the safety and functionality of critical structures.
Some of the most common issues that marine and offshore equipment faces include:
Corrosion: The primary cause of material degradation in saltwater environments. Corrosion attacks metal surfaces, weakening their structure and leading to potential failures.
Fatigue: Repeated stresses and strains from waves, weather, and operational activity can lead to fatigue cracks in critical components such as ship hulls, risers, and offshore platform supports.
Weld Integrity: Welding defects such as porosity, cracks, and lack of fusion can lead to weak points in structures, particularly in offshore rigs and ships subjected to high stress.
Cavitation: The formation and collapse of air bubbles in liquids can cause erosion damage to components like propellers, pump components, and turbines.
Effective inspections using NDT methods help identify such issues early, reducing the likelihood of failures and enhancing the longevity of marine and offshore assets.
NDT Methods Used in Marine & Offshore Inspections
Various NDT techniques are employed to detect defects and assess the condition of marine and offshore infrastructure. These methods provide invaluable information about the integrity of equipment and structures, ensuring that repairs or maintenance can be scheduled proactively to minimize downtime.
1. Ultrasonic Testing (UT)
Ultrasonic Testing (UT) is one of the most widely used NDT methods in the marine and offshore sectors due to its ability to detect both surface and subsurface defects. High-frequency sound waves are transmitted into the material, and the reflected waves are analyzed to detect any discontinuities or anomalies. In marine and offshore inspections, UT is used for:
Detecting corrosion and wall thinning in pipelines, tanks, and hulls.
Evaluating welds in critical components like pressure vessels, risers, and structural beams.
Assessing the condition of subsea equipment like risers and umbilicals.
Advanced techniques such as Phased Array Ultrasonic Testing (PAUT) offer improved imaging resolution and more accurate detection of complex defects.
2. Magnetic Particle Testing (MPT)
Magnetic Particle Testing (MPT) is used to detect surface and near-surface defects in ferromagnetic materials. In this method, a magnetic field is applied to the material, and fine magnetic particles are used to reveal any surface defects. MPT is commonly used in marine and offshore industries for:
Inspecting welds and critical joints for cracks and other surface-breaking defects.
Evaluating structural components such as ship hulls, offshore platform supports, and risers for signs of stress or damage.
Detecting fatigue cracks in components subjected to repetitive stress, such as propellers and valves.
MPT is particularly useful for identifying issues that are not visible to the naked eye, such as hairline cracks in metal structures.
3. Eddy Current Testing (ECT)
Eddy Current Testing (ECT) is an NDT method used to detect surface and near-surface defects in conductive materials. It works by inducing a magnetic field into the material, creating electrical currents (eddy currents) that interact with any imperfections. ECT is used in marine and offshore inspections for:
Assessing material thickness and detecting corrosion or wear in metallic structures.
Inspecting heat exchangers, pressure vessels, and pipelines for cracks, corrosion, or fatigue.
Evaluating underwater equipment, including hulls, for signs of damage or degradation.
ECT is particularly useful in inspecting thin-walled structures and components that are difficult to access, such as underwater pipes and pressure vessels.
4. Radiographic Testing (RT)
Radiographic Testing (RT) uses X-rays or gamma rays to examine the internal structure of materials. This technique produces high-resolution images that reveal internal defects such as cracks, voids, or inclusions. RT is commonly used in the marine and offshore industries to:
Inspect welded joints in critical areas such as ship hulls, offshore platform structures, and risers for internal defects.
Evaluate subsea pipelines for internal corrosion, cracks, and other potential issues.
Examine pressure vessels and tanks for signs of fatigue, corrosion, or stress-related damage.
The ability to see inside materials without disassembling them makes RT an invaluable tool for ensuring the integrity of offshore equipment.
5. Visual Testing (VT)
Visual Testing (VT) is one of the simplest and most cost-effective NDT methods, yet it remains a vital part of marine and offshore inspections. By performing a visual examination of components, technicians can identify visible signs of wear, corrosion, or damage. VT is often used to:
Inspect external surfaces of ships, platforms, and subsea structures for cracks, corrosion, or other surface damage.
Monitor for leaks in pipelines, tanks, and risers that could lead to environmental contamination or loss of pressure.
Evaluate equipment in hard-to-reach areas such as underwater or high-altitude locations.
VT can be performed on-site with the aid of drones or remotely operated vehicles (ROVs), making it an adaptable and valuable method for both regular inspections and emergency assessments.
6. Dye Penetrant Testing (DPT)
Dye Penetrant Testing (DPT) is used to reveal surface-breaking defects in non-porous materials. The process involves applying a liquid dye to the surface of the component, then removing excess dye and applying a developer to make the defects visible under UV light. In marine and offshore inspections, DPT is used to:
Inspect welds and joints for surface cracks, fatigue, and other defects.
Detect leaks in tanks, pipelines, and pressure vessels.
Evaluate critical structural components such as support beams, risers, and propellers for cracks and damage.
DPT is particularly useful in detecting small or hairline cracks that could otherwise go unnoticed.
Benefits of NDT in Marine & Offshore Industries
The implementation of NDT in marine and offshore inspections provides numerous benefits, including:
Improved Safety: Regular inspections help detect defects early, reducing the risk of failures that could lead to accidents, environmental damage, or loss of life.
Cost Savings: By identifying problems early, NDT helps prevent costly repairs, replacements, and unscheduled downtime.
Regulatory Compliance: NDT ensures compliance with international safety standards and industry regulations, including those set by bodies like the International Maritime Organization (IMO) and various classification societies.
Operational Efficiency: NDT minimizes disruptions to operations, allowing for more efficient inspections, faster turnaround times, and longer operational lifecycles for offshore assets.
Extended Asset Life: Proactive inspections using NDT help extend the lifespan of vessels, offshore platforms, and subsea equipment by identifying and addressing issues before they become critical.
Conclusion
Non-Destructive Testing (NDT) plays a pivotal role in maintaining the safety, reliability, and integrity of marine and offshore assets. With techniques like Ultrasonic Testing (UT), Magnetic Particle Testing (MPT), Eddy Current Testing (ECT), and Radiographic Testing (RT), NDT provides essential insights into the condition of critical infrastructure, allowing for timely interventions and repairs.
At NDT AND PWHT SOLUTIONS PVT LTD (India), we specialize in providing cutting-edge NDT services tailored to the needs of the marine and offshore industries. Our advanced techniques and experienced team help ensure that your operations remain safe, efficient, and compliant with the highest industry standards.
By incorporating NDT into routine maintenance and inspection schedules, marine and offshore operators can ensure that their assets perform optimally, mitigating risks and maximizing the lifespan of their equipment.