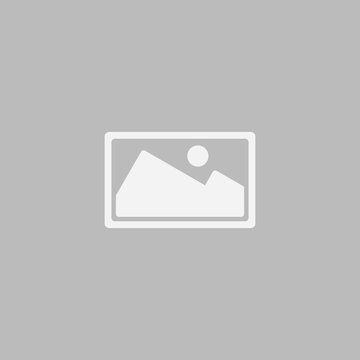
The Role of NDT in Aerospace Inspections
Introduction
The aerospace industry is one of the most high-stakes sectors in terms of safety and operational integrity. Aircraft and spacecraft must undergo rigorous inspections to ensure that all components meet the highest standards of quality and performance. This is because even the smallest defect or failure can have catastrophic consequences in terms of human safety, financial loss, and environmental impact.
Non-Destructive Testing (NDT) is crucial in aerospace inspections as it allows for the detection of material flaws and structural weaknesses without causing any damage to the components being tested. NDT techniques are indispensable in maintaining the safety, efficiency, and reliability of aerospace systems, ensuring compliance with aviation standards, and extending the lifespan of aircraft.
This article highlights the importance of NDT in aerospace inspections, the methods commonly used, and their application in ensuring the safety of aircraft and aerospace components.
The Importance of NDT in Aerospace Inspections
Aerospace components are subjected to extreme forces and environmental conditions during flight. They must endure high speeds, pressure fluctuations, temperature variations, and mechanical stresses. These challenges, along with the critical nature of the components, make frequent and thorough inspections essential.
The main concerns in aerospace inspections include:
Fatigue and Stress Cracks: Components such as wings, fuselages, and landing gear experience repeated stress and load cycles, which can lead to the development of fatigue cracks.
Corrosion: Exposure to moisture, salt, and chemicals can cause corrosion, especially in high-stress areas such as engine parts, wings, and joints.
Manufacturing Defects: During production, materials may have imperfections, such as voids, inclusions, or misalignments, that can compromise the integrity of the component.
Weld Integrity: Welds in critical components must be free of defects such as porosity, cracks, and incomplete fusion to prevent failure.
NDT enables the detection of these issues before they lead to failures, ensuring the safe operation of aircraft and aerospace systems.
NDT Methods Used in Aerospace Inspections
Several NDT techniques are used in aerospace inspections to detect flaws in materials and structures. Each method is chosen based on the specific requirements of the component being inspected, the type of material, and the nature of the inspection.
1. Ultrasonic Testing (UT)
Ultrasonic Testing (UT) is one of the most widely used NDT methods in aerospace. It uses high-frequency sound waves that are transmitted into the material and reflected back to detect internal defects such as cracks, voids, or inclusions. UT is used in aerospace to:
Inspect critical components such as turbine blades, wing spars, and engine parts for internal defects.
Detect fatigue cracks and material degradation in high-stress areas like landing gear and fuselages.
Check for bonding integrity in composite materials used in modern aircraft.
Advanced UT techniques, such as Phased Array Ultrasonic Testing (PAUT) and Time-of-Flight Diffraction (TOFD), provide high-resolution imaging and improved defect characterization, making them ideal for complex aerospace applications.
2. Eddy Current Testing (ECT)
Eddy Current Testing (ECT) is commonly used in aerospace to detect surface and near-surface defects in conductive materials. ECT uses electromagnetic induction to generate currents (eddy currents) in the material, which can then be analyzed to reveal irregularities. In aerospace, ECT is used for:
Inspecting aircraft fuselages and wing structures for corrosion, cracks, and other surface defects.
Evaluating fasteners and rivets for signs of wear, corrosion, or cracks.
Testing turbine blades, engine components, and heat exchangers for material degradation.
ECT is particularly useful for inspecting thin-walled materials and detecting issues in areas that are difficult to access, such as inside turbine engines.
3. Magnetic Particle Testing (MPT)
Magnetic Particle Testing (MPT) is primarily used for inspecting ferromagnetic materials for surface and near-surface defects. This technique is highly effective in detecting cracks, laps, and other surface-breaking defects. In aerospace, MPT is applied to:
Inspecting high-stress components such as engine parts, landing gear, and structural supports for cracks and fatigue.
Evaluating welded joints and fasteners that are critical for the structural integrity of aircraft.
Detecting stress-related cracks and corrosion in various metallic components, particularly in critical areas such as wings and engine assemblies.
MPT is ideal for identifying visible defects that could compromise the performance and safety of aircraft.
4. Radiographic Testing (RT)
Radiographic Testing (RT) uses X-rays or gamma rays to examine the internal structure of materials. The radiation passes through the material and exposes a film, producing an image that reveals internal defects. RT is widely used in aerospace for:
Inspecting welded joints and metal components for internal defects such as cracks, porosity, and inclusions.
Evaluating composite materials for internal bonding integrity and hidden delaminations.
Checking the quality of castings and forgings used in engine components, airframes, and landing gear.
RT provides high-resolution images that can reveal defects that are not visible through surface inspection methods.
5. Visual Testing (VT)
Visual Testing (VT) is one of the simplest and most cost-effective NDT methods, but it remains crucial in aerospace inspections. A detailed visual examination can often reveal surface defects such as cracks, corrosion, or other damage. VT is commonly used in:
Inspecting external surfaces of aircraft for signs of damage, corrosion, or wear, particularly around rivets, fasteners, and joints.
Monitoring for leaks in critical systems, such as hydraulic lines, fuel tanks, and cooling systems.
Assessing the overall condition of components like wings, engines, and fuselages during routine inspections.
VT is particularly useful for initial inspections and for identifying areas that require more in-depth NDT.
6. Dye Penetrant Testing (DPT)
Dye Penetrant Testing (DPT) is a surface inspection technique that uses a liquid dye to reveal surface-breaking defects in non-porous materials. The dye is applied to the surface, and after a waiting period, excess dye is removed, leaving the defect visible under UV or visible light. DPT is used in aerospace for:
Inspecting high-stress areas such as engine components, turbine blades, and airframes for cracks and fatigue.
Detecting weld defects in critical joints, such as those found in fuselages, wings, and landing gear.
Evaluating fasteners, rivets, and other hardware for potential flaws that could compromise the structural integrity of the aircraft.
DPT is particularly effective at identifying small surface cracks that may not be visible to the naked eye.
Benefits of NDT in Aerospace Inspections
NDT provides several benefits for aerospace inspections, including:
Enhanced Safety: By detecting defects early, NDT helps prevent catastrophic failures and ensures that aircraft remain safe and airworthy throughout their operational lifespan.
Cost Savings: NDT minimizes downtime and reduces the need for expensive repairs or replacements by identifying potential issues before they escalate.
Compliance with Regulations: NDT ensures compliance with aviation safety standards set by regulatory bodies such as the Federal Aviation Administration (FAA) and the European Union Aviation Safety Agency (EASA).
Extended Equipment Lifespan: Regular NDT inspections help extend the life of aircraft components by identifying and addressing issues before they compromise the integrity of the structure.
Operational Efficiency: NDT allows for efficient, non-intrusive inspections, minimizing the impact on flight schedules and reducing operational disruptions.
Conclusion
Non-Destructive Testing (NDT) is an essential part of ensuring the safety, reliability, and longevity of aerospace components. Techniques such as Ultrasonic Testing (UT), Eddy Current Testing (ECT), Magnetic Particle Testing (MPT), Radiographic Testing (RT), and Dye Penetrant Testing (DPT) are vital for detecting defects, ensuring quality control, and maintaining compliance with stringent industry regulations.
At NDT AND PWHT SOLUTIONS PVT LTD (India), we provide advanced NDT services to the aerospace industry, helping ensure the safety and reliability of aircraft and aerospace components. By using state-of-the-art technologies and experienced personnel, we ensure that aerospace operators can maintain the highest standards of safety and operational excellence.
Regular NDT inspections are key to minimizing risks, preventing failures, and maximizing the lifespan of aerospace assets. With our expertise in NDT, we are committed to supporting the aerospace industry in its mission to deliver safe and reliable transportation.