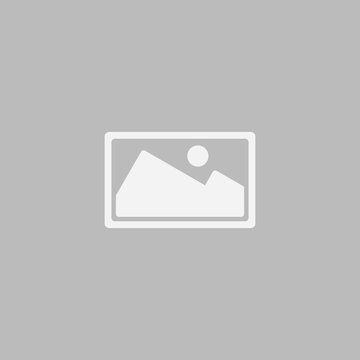
The Role of NDT in Aerospace Industry Inspections
Introduction
The aerospace industry is synonymous with precision, safety, and reliability. From commercial airliners to military aircraft and spacecraft, the stakes are incredibly high. Even the smallest defect in an aircraft’s structure or components can lead to catastrophic failure. As a result, non-destructive testing (NDT) plays a pivotal role in ensuring the safety and performance of aerospace systems.
This article explores the crucial role NDT plays in aerospace inspections, highlighting the various techniques used and their applications across different sectors of the industry, including manufacturing, maintenance, and in-service inspection of aircraft, space vehicles, and their components.
The Importance of NDT in Aerospace Industry
The aerospace industry is particularly reliant on materials that undergo extreme conditions, such as high stresses, vibrations, and temperature variations. These conditions can cause materials to degrade or develop defects that may not be visible to the naked eye. Key challenges in aerospace components include:
Fatigue Cracks: Repeated loading and unloading cycles can lead to cracks in critical parts such as wing spars, fuselage, and engine components.
Corrosion: Exposure to the elements, including moisture, salt, and chemicals, can lead to corrosion of metallic and composite parts, weakening the structure.
Impact Damage: Foreign Object Damage (FOD) is a significant concern in the aerospace industry, with even small impacts potentially compromising safety.
Weld and Bond Integrity: Components in the aerospace industry are often welded or bonded together, and defects in these connections can cause failure under load.
NDT is indispensable for detecting such defects early, ensuring that the aircraft or spacecraft remains safe and operational throughout its lifecycle.
NDT Methods in Aerospace Industry
Several NDT methods are employed to detect defects in aerospace materials, ranging from conventional techniques to cutting-edge technologies. These methods are used throughout an aircraft’s lifecycle, from the manufacturing stage to routine maintenance and in-service inspections.
1. Ultrasonic Testing (UT)
Ultrasonic Testing (UT) is widely used in the aerospace industry due to its ability to detect both surface and subsurface defects in materials. UT works by sending high-frequency sound waves into the material and analyzing the reflections to detect discontinuities. In aerospace, UT is used for:
Detecting cracks in critical structural components such as wings, fuselage, and engine parts.
Measuring material thickness to assess corrosion or wear, especially in aging aircraft.
Inspecting welds and bonds in aerospace structures for signs of porosity, cracks, and inclusions.
With the advent of advanced techniques like Phased Array Ultrasonic Testing (PAUT), UT now provides high-resolution imaging, allowing for more accurate defect detection and characterization.
2. Eddy Current Testing (ECT)
Eddy Current Testing (ECT) is another vital method in aerospace inspections. ECT uses electromagnetic induction to detect surface and near-surface defects in conductive materials. In aerospace, ECT is primarily used to:
Inspect metallic components such as turbine blades, wing structures, and fuselage for cracks or corrosion.
Examine tight or difficult-to-reach areas where other methods might not be effective.
Detect material degradation such as fatigue cracks, corrosion, or thinning in highly stressed components like landing gear.
ECT is particularly valuable for inspecting aluminum, titanium, and other non-ferrous alloys commonly used in aerospace applications.
3. Radiographic Testing (RT)
Radiographic Testing (RT) uses X-rays or gamma rays to inspect the internal structure of materials. In aerospace, RT is used to:
Inspect welds and joints for hidden defects such as porosity, cracks, and inclusions.
Examine critical components like turbine blades, landing gear, and airframe structures to ensure they meet quality and safety standards.
Assess internal bonding in composite materials and adhesive joints, which are critical for modern aerospace structures.
RT provides high-resolution images that allow inspectors to identify minute defects that are not visible through other NDT methods. Digital radiography (DR) has further enhanced RT by reducing exposure times and improving image quality.
4. Magnetic Particle Testing (MPT)
Magnetic Particle Testing (MPT) is a widely used NDT method for detecting surface and near-surface defects in ferromagnetic materials. In aerospace, MPT is applied to:
Inspect structural components such as wing spars, turbine blades, and engine parts for cracks and other surface defects.
Examine critical safety items such as fasteners, bolts, and joints for signs of fatigue or stress fractures.
MPT is particularly effective for inspecting components that are subjected to high-stress conditions and is a commonly used method for detecting cracks in metallic parts.
5. Dye Penetrant Testing (DPT)
Dye Penetrant Testing (DPT) is a low-cost and effective NDT method used to detect surface-breaking defects in non-porous materials. In aerospace, DPT is used for:
Inspecting small or complex components such as turbine blades, castings, and fasteners.
Detecting surface cracks that could compromise the structural integrity of components.
Evaluating components that are difficult to inspect using other methods due to shape or size.
DPT is ideal for detecting surface cracks and is often used in combination with other NDT techniques for comprehensive inspections.
6. Visual Testing (VT)
Visual Testing (VT) is the most basic form of NDT but remains an essential tool for aerospace inspections. VT involves a visual examination of components to detect visible signs of wear, damage, or defects. In aerospace, VT is used to:
Perform routine inspections of external components such as wings, fuselage, and control surfaces.
Inspect for Foreign Object Damage (FOD), which can be a major concern in aircraft operations.
Check for signs of corrosion, wear, or fatigue on structural components and fasteners.
VT is often used in combination with other NDT methods to provide a complete assessment of the condition of an aircraft or spacecraft.
The Benefits of NDT in Aerospace Industry
Ensuring Safety: NDT helps identify potential failures before they occur, ensuring the safety of passengers and crew by preventing catastrophic accidents.
Maintaining Structural Integrity: Regular inspections using NDT methods ensure that critical components like wings, fuselage, and engine parts remain structurally sound throughout the lifecycle of an aircraft.
Minimizing Downtime: By detecting defects early, NDT allows for timely repairs and maintenance, reducing unplanned downtime and improving the operational efficiency of aerospace companies.
Compliance with Regulatory Standards: NDT ensures compliance with stringent regulatory requirements from organizations like the Federal Aviation Administration (FAA) and the European Union Aviation Safety Agency (EASA), which set safety and inspection standards for the aerospace industry.
Cost Savings: By identifying defects early, NDT prevents costly repairs and replacements, extending the lifespan of expensive aerospace components and systems.
Conclusion
Non-Destructive Testing plays an integral role in maintaining the safety, reliability, and performance of aerospace vehicles and components. From manufacturing to routine maintenance and in-service inspections, NDT ensures that the highest safety standards are met in the aerospace industry. Advanced techniques such as Ultrasonic Testing (UT), Eddy Current Testing (ECT), Radiographic Testing (RT), Magnetic Particle Testing (MPT), and Dye Penetrant Testing (DPT) provide comprehensive defect detection capabilities, while innovations like Phased Array Ultrasonic Testing (PAUT) and Digital Radiography (DR) continue to enhance inspection efficiency and accuracy.
At NDT AND PWHT SOLUTIONS PVT LTD (India), we leverage state-of-the-art NDT technologies to provide precise and reliable inspection services for the aerospace sector. Our experienced team is committed to delivering high-quality, non-invasive solutions that help ensure the safety and longevity of aerospace assets.
By incorporating NDT into regular inspection schedules, aerospace companies can maintain operational safety, minimize risks, and comply with industry regulations, ultimately contributing to the advancement of the aerospace industry.