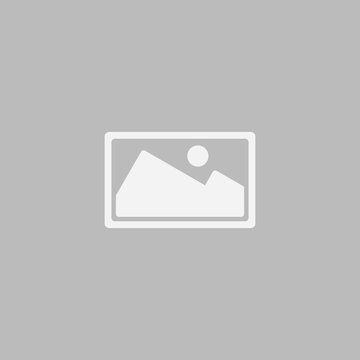
The Role of NDT in Aerospace: Aircraft Component Testing
Introduction
In the aerospace industry, ensuring the safety, performance, and longevity of aircraft components is paramount. Non-Destructive Testing (NDT) methods are essential in detecting potential defects and material degradation without causing damage to the components. Aircraft undergo rigorous inspection processes at various stages of their lifecycle, from initial production to ongoing maintenance and after-service checks.
At NDT AND PWHT SOLUTIONS PVT LTD (India), we specialize in providing advanced NDT services for the aerospace sector, ensuring that aircraft components meet the highest standards of safety and reliability. This article delves into the importance of NDT in aircraft component testing and highlights the primary NDT methods used in aerospace inspections.
The Importance of Aircraft Component Testing
Aircraft components are subject to a wide range of stresses, including thermal cycles, vibration, corrosion, and mechanical forces. Over time, these factors can lead to fatigue, wear, and the formation of cracks or other defects that could compromise the aircraft’s safety and performance.
Regular and thorough inspections using NDT methods are crucial to ensure that these components are free from critical defects. This is especially important in areas such as:
Structural components: Wings, fuselage, tail sections, and landing gears.
Engine components: Turbines, compressors, shafts, and casings.
Composite materials: Used increasingly in modern aircraft, these materials require specialized testing to detect issues like delamination or bonding defects.
NDT methods help to:
Ensure the structural integrity and reliability of aircraft components.
Detect fatigue cracks, corrosion, and other failures that could impact performance and safety.
Minimize the risk of costly repairs or catastrophic failures.
Comply with stringent aviation regulations and certification standards.
Common NDT Methods Used in Aerospace Component Testing
1. Ultrasonic Testing (UT)
Ultrasonic Testing (UT) is one of the most common NDT methods used in aerospace applications. UT uses high-frequency sound waves to detect internal and surface defects in components. It is especially useful for:
Detecting fatigue cracks in metallic and composite materials.
Measuring wall thickness of structural components like fuselage and wings.
Identifying flaws in welded joints and turbine engine parts.
Phased Array Ultrasonic Testing (PAUT), an advanced form of UT, allows for faster and more accurate inspections by using multiple ultrasonic beams and providing real-time imaging of defects.
2. Eddy Current Testing (ECT)
Eddy Current Testing (ECT) is a non-invasive method that uses electromagnetic induction to detect surface and near-surface defects in conductive materials. In the aerospace industry, ECT is often used for:
Inspection of cracks on aircraft skin, engine components, and landing gear.
Detection of corrosion in aircraft structures and components.
Testing of thin-walled parts and welds that are difficult to inspect using other methods.
ECT provides high sensitivity to small surface cracks, making it ideal for inspecting high-stress areas in aerospace components.
3. Radiographic Testing (RT)
Radiographic Testing (RT) uses X-rays or gamma rays to produce detailed images of the internal structure of a component. RT is highly effective for:
Inspecting welded joints and seams in metallic parts.
Detecting internal defects such as porosity, cracks, and voids.
Evaluating the integrity of complex components, such as turbine blades and engine casings.
Digital Radiography (DR) offers enhanced imaging capabilities, allowing for faster analysis and easier archiving of inspection data.
4. Magnetic Particle Testing (MPT)
Magnetic Particle Testing (MPT) is used for detecting surface and near-surface cracks in ferromagnetic materials. In aerospace applications, MPT is particularly useful for:
Inspection of landing gear components, which are exposed to high stresses during takeoff and landing.
Testing engine parts such as shafts, gears, and housings.
Identifying cracks in critical structural components like wing spars and fuselage.
MPT is a quick and effective method, particularly in identifying surface defects that could lead to failure under stress.
5. Visual Testing (VT)
Visual Testing (VT) is the simplest and most widely used NDT method in the aerospace industry. It involves a visual inspection of the aircraft components to identify any obvious defects such as cracks, corrosion, or wear. VT is essential for:
Routine checks during pre-flight inspections.
Assessing the condition of engine components, landing gear, and wings.
Identifying surface wear on high-stress areas like turbine blades and airframes.
While VT is not as detailed as other NDT methods, it serves as an effective initial screening tool and can often highlight areas that require more advanced testing.
Benefits of NDT in Aerospace Component Testing
Safety Assurance: Regular NDT inspections help to identify potential risks and ensure that components are safe for use, preventing catastrophic failures that could endanger passengers or crew.
Cost-Effectiveness: NDT methods provide early detection of defects, enabling timely maintenance and reducing the cost of repairs or component replacements.
Extended Component Life: By identifying and addressing defects early, NDT helps extend the operational life of critical components, ensuring that aircraft remain in service for longer periods.
Compliance with Aviation Regulations: NDT is essential for meeting strict aviation safety standards and certification requirements, such as those set by the FAA (Federal Aviation Administration) and EASA (European Union Aviation Safety Agency).
Minimized Downtime: Efficient NDT methods reduce the need for lengthy inspections or disassembly of aircraft components, allowing for quicker turnaround times and minimal operational disruption.
Conclusion
Non-Destructive Testing is indispensable in the aerospace industry, ensuring that aircraft components are free from defects and meet the highest safety standards. At NDT AND PWHT SOLUTIONS PVT LTD (India), we leverage the latest NDT technologies to provide accurate and reliable testing services for the aerospace sector.
Our advanced NDT services, including Ultrasonic Testing (UT), Eddy Current Testing (ECT), Radiographic Testing (RT), Magnetic Particle Testing (MPT), and Visual Testing (VT), help ensure the safety, efficiency, and longevity of aircraft components. By incorporating the latest innovations in NDT, we help our clients maintain safe, high-performance fleets that meet the stringent requirements of the aviation industry.