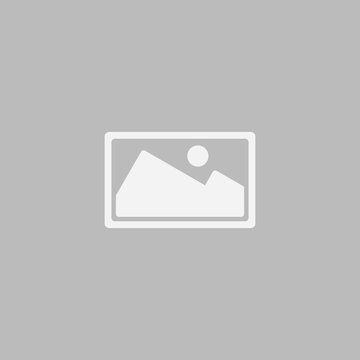
The Importance of NDT in Power Generation: Turbine and Boiler Inspections.
Introduction
The power generation industry relies on the uninterrupted operation of complex machinery such as turbines, boilers, and heat exchangers to ensure consistent and efficient energy production. These critical components are subject to immense operational stresses, including high temperatures, pressure variations, and mechanical forces, which can lead to material degradation, fatigue, and failure over time.
Non-Destructive Testing (NDT) plays a crucial role in the maintenance and inspection of these components, ensuring their safety, efficiency, and longevity without causing any damage. At NDT AND PWHT SOLUTIONS PVT LTD (India), we provide advanced NDT services tailored to the power generation sector, with a focus on turbine and boiler inspections. This article explores the importance of NDT in the power generation industry and the methods used to assess the integrity of these essential components.
The Role of NDT in Power Generation
In power plants, turbines and boilers are two of the most critical components. Turbines are responsible for converting thermal energy into mechanical energy, while boilers provide the steam needed to drive turbines and other machinery. Over time, both turbines and boilers are exposed to extreme operating conditions that can lead to fatigue, corrosion, erosion, and other forms of damage. Early detection of these issues is essential to prevent catastrophic failures, extend the operational life of these components, and minimize downtime for repairs.
NDT offers a non-invasive way to inspect these components, providing accurate and reliable results without interrupting their operation. By using advanced NDT techniques, operators can detect hidden flaws, assess material integrity, and ensure that these components are operating within safe parameters.
Common NDT Methods Used in Power Generation
1. Ultrasonic Testing (UT)
Ultrasonic Testing (UT) is one of the most widely used NDT methods in the power generation industry. UT uses high-frequency sound waves to detect internal flaws, measure thickness, and assess the overall integrity of components. In turbine and boiler inspections, UT is used to:
Detect cracks and voids in turbine blades, casings, and rotor shafts.
Measure the wall thickness of boiler tubes to assess the effects of corrosion or erosion.
Identify material degradation caused by thermal cycling, pressure fluctuations, or fatigue.
Advanced techniques like Phased Array Ultrasonic Testing (PAUT) can provide detailed imaging and higher accuracy, enabling more precise inspection of complex geometries and difficult-to-reach areas.
2. Eddy Current Testing (ECT)
Eddy Current Testing (ECT) is particularly effective for inspecting the surface and near-surface regions of conductive materials. In the power generation industry, ECT is commonly used to detect:
Surface cracks in turbine blades, generator shafts, and other critical components.
Corrosion and pitting in boiler tubes, heat exchangers, and pressure vessels.
Wear and erosion on surfaces subject to high stresses, such as turbine rotors and bearings.
ECT is especially beneficial for inspecting components that are difficult to reach with other NDT methods, as it can detect surface defects without requiring physical contact.
3. Radiographic Testing (RT)
Radiographic Testing (RT) uses X-rays or gamma rays to produce images of the internal structure of materials. RT is particularly useful for detecting:
Weld defects in boiler tubes, turbine casings, and pressure vessels.
Internal cracks and voids in high-stress areas such as turbine blades and rotors.
Porosity and inclusions in metallic components.
RT is ideal for inspecting welded joints and other critical areas that may be hidden from visual inspection. Digital Radiography (DR) provides enhanced imaging, allowing for faster analysis and easier data management.
4. Magnetic Particle Testing (MPT)
Magnetic Particle Testing (MPT) is used to detect surface and near-surface defects in ferromagnetic materials. In power plants, MPT is commonly applied to:
Inspect turbine rotor shafts for cracks or surface flaws.
Examine boiler tube welds and other structural components for signs of fatigue.
Identify corrosion or stress cracks on critical parts of turbine generators.
MPT is a quick and effective method for inspecting ferrous components, providing immediate results that can guide further testing or maintenance decisions.
5. Visual Testing (VT)
Visual Testing (VT) is one of the simplest and most widely used NDT methods. It involves direct observation of components for visible signs of damage or wear. In power generation, VT is used to:
Inspect turbine blades, casings, and seals for cracks, corrosion, or foreign object damage.
Check boiler tubes for external damage, such as cracks, pitting, or wear.
Monitor the condition of insulation, valves, and other critical components.
While VT does not provide the depth of information that other methods offer, it serves as an effective first step in identifying potential issues and determining which components require more detailed examination.
Benefits of NDT in Power Generation
Safety Assurance: NDT methods ensure that turbines and boilers remain free from critical defects, preventing unexpected failures that could compromise the safety of the power plant and its personnel.
Cost-Effective Maintenance: By detecting problems early, NDT allows for timely repairs, reducing the need for costly replacements or major overhauls.
Extended Equipment Life: Regular NDT inspections help maintain the operational integrity of turbines and boilers, extending their lifespan and reducing the frequency of replacements.
Operational Efficiency: NDT enables power plants to operate at optimal efficiency by identifying and addressing issues that could cause performance degradation or reduced output.
Regulatory Compliance: Regular inspections using NDT are often required to meet industry regulations and standards, ensuring that power generation facilities operate in compliance with safety and environmental guidelines.
Conclusion
Non-Destructive Testing is a vital component of ensuring the safety, reliability, and efficiency of turbines, boilers, and other critical components in the power generation industry. By using advanced NDT methods such as Ultrasonic Testing (UT), Eddy Current Testing (ECT), Radiographic Testing (RT), Magnetic Particle Testing (MPT), and Visual Testing (VT), power plants can detect potential flaws before they lead to failures, thereby avoiding costly repairs and downtime.
At NDT AND PWHT SOLUTIONS PVT LTD (India), we specialize in providing advanced NDT services for the power generation sector, helping our clients maintain high-performance and long-lasting turbines and boilers. With our expertise in NDT, we ensure that power plants operate efficiently, safely, and in compliance with industry standards.