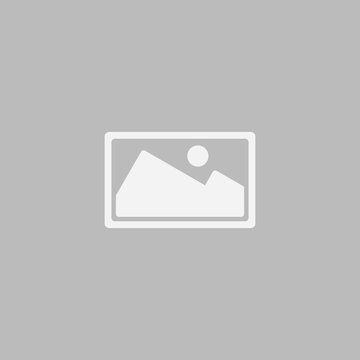
Successful Implementation of Time of Flight Diffraction (TOFD) in Power Plants
Introduction
Time of Flight Diffraction (TOFD) is a widely recognized Non-Destructive Testing (NDT) technique known for its accuracy in detecting and sizing defects in welds and structural components. In the power generation industry, where structural integrity is critical, TOFD plays a vital role in ensuring safety, reliability, and operational efficiency.
At NDT AND PWHT SOLUTIONS PVT LTD (India), we specialize in implementing TOFD for power plant inspections, offering precise defect characterization, minimal false indications, and comprehensive reporting. This article highlights the successful application of TOFD in power plants and its benefits for the industry.
Understanding Time of Flight Diffraction (TOFD)
TOFD is an advanced ultrasonic testing method that relies on diffracted sound waves from defect edges rather than just reflection, allowing for more accurate defect detection and sizing. The technique consists of:
– A pair of transducers positioned on opposite sides of the weld
– A transmitted ultrasonic wave that propagates through the material
– Diffraction signals from defect tips that provide precise flaw characterization
Key Advantages of TOFD in Power Plants:
– High Accuracy in Defect Sizing – TOFD can detect and size cracks as small as 0.5mm with minimal error.
– Fast Inspection Rates – Covers large areas quickly, reducing downtime.
– Comprehensive Data Capture – Enables post-analysis and long-term integrity monitoring.
– Minimized False Indications – More reliable than conventional UT and radiographic testing.
TOFD Applications in Power Plants
1.Boiler Tube and Pressure Vessel Inspection
Boilers and pressure vessels in power plants operate under extreme conditions. TOFD ensures early detection of stress-related cracks, corrosion damage, and weld defects, preventing catastrophic failures.
2.Turbine Blade and Rotor Integrity Assessment
Turbines are subjected to cyclic stress, which can cause fatigue cracks. TOFD allows for precise detection of these cracks before they reach critical failure points.
3.Piping System Integrity Monitoring
Power plant piping systems carry high-pressure steam and fluids. TOFD is ideal for detecting weld defects, corrosion, and erosion damage, ensuring long-term reliability.
4.Structural Weld Inspection
From steel frameworks to reactor containment structures, TOFD is used to assess welding quality and structural soundness, ensuring compliance with industry standards.
Case Study: TOFD Success in a Thermal Power Plant
A leading thermal power plant in India approached NDT AND PWHT SOLUTIONS PVT LTD for an inspection solution after experiencing unexpected shutdowns due to weld failures in its high-pressure steam piping. Our TOFD-based inspection revealed multiple micro-cracks that were previously undetectable using conventional UT methods.
Results Achieved:
– Defect Detection Accuracy Improved by 40%
– Shutdowns Reduced by 30% Through Early Defect Detection
– Enhanced Safety and Compliance with Industry Standards
The Future of TOFD in Power Plants
With advancements in automated TOFD scanning, AI-based defect analysis, and data-driven predictive maintenance, the role of TOFD in power plant NDT will continue to expand.
At NDT AND PWHT SOLUTIONS PVT LTD (India), we are committed to providing state-of-the-art TOFD solutions to help power plants maintain efficiency, safety, and compliance with industry regulations.
Conclusion
The successful implementation of TOFD in power plants has revolutionized weld inspection, defect detection, and asset integrity management. By utilizing TOFD, power plant operators can enhance safety, reduce downtime, and extend the lifespan of critical components.
For expert TOFD services and advanced NDT solutions, contact NDT AND PWHT SOLUTIONS PVT LTD today!