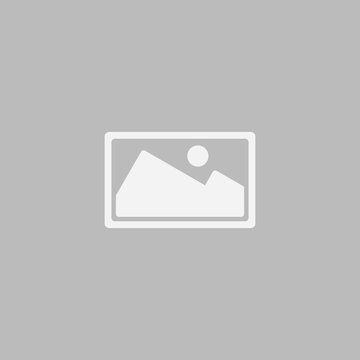
Radiographic Testing (RT) in NDT: Principles, Techniques, and Applications.
Introduction
Radiographic Testing (RT) is one of the most powerful Non-Destructive Testing (NDT) methods used for detecting internal defects in materials and welded structures. By utilizing X-rays or gamma rays, RT provides highly detailed images of internal discontinuities that may not be visible using other inspection techniques. It is widely used in industries such as oil & gas, aerospace, power generation, marine, and heavy engineering to ensure structural integrity and safety.
At NDT AND PWHT SOLUTIONS PVT LTD (India), we employ state-of-the-art RT technologies to deliver precise and reliable inspection services. This article explores the principles, techniques, advantages, and applications of Radiographic Testing.
What is Radiographic Testing (RT)?
Radiographic Testing (RT) is a penetrant inspection method that uses ionizing radiation (X-rays or gamma rays) to penetrate materials and capture images of their internal structure on film or digital sensors. These radiographic images help identify defects such as cracks, porosity, inclusions, lack of fusion, and voids within a component or weld.
How RT Works:
A radiation source (X-ray tube or gamma-ray source) emits high-energy radiation.
The radiation passes through the test object.
A film or digital detector captures the transmitted rays.
The variations in radiation absorption create an image that reveals internal flaws.
A qualified inspector analyzes the image to detect and evaluate defects.
Types of Radiographic Testing (RT)
1. X-Ray Radiography (X-Ray RT)
Uses an X-ray tube to generate radiation.
Best for thin materials such as aluminum, plastics, and composites.
Common in aerospace, medical, and precision engineering applications.
2. Gamma Radiography (Gamma RT)
Uses radioactive isotopes such as Iridium-192, Selenium-75, or Cobalt-60.
Ideal for inspecting thicker materials, such as pipelines, pressure vessels, and structural steel.
Suitable for remote field inspections where X-ray machines are impractical.
3. Digital Radiography (DR)
Replaces traditional film with digital detectors for real-time imaging.
Offers faster processing, enhanced contrast, and automated defect detection.
Widely used in industries requiring high-precision inspections.
4. Computed Radiography (CR)
Uses phosphor imaging plates instead of traditional film.
Provides digital enhancement capabilities and higher resolution than conventional film radiography.
Efficient for applications requiring high-volume inspections.
5. Computed Tomography (CT)
Produces 3D images of internal structures by combining multiple radiographic images.
Used for complex inspections in aerospace, medical, and precision manufacturing industries.
Detects micro-cracks, voids, and internal material variations with extreme precision.
Advantages of Radiographic Testing (RT)
1. Detects Internal Defects
RT is capable of revealing defects inside the material, making it ideal for welds, castings, and complex structures.
2. Provides Permanent Records
Radiographic images (films or digital scans) serve as permanent inspection records for future reference and quality control.
3. Highly Accurate
RT offers high-resolution imaging, enabling detailed analysis and precise defect characterization.
4. Non-Destructive
RT does not alter or damage the tested material, allowing it to remain in service after inspection.
5. Works on Various Materials
RT can be applied to metals, composites, plastics, and ceramics, making it versatile across industries.
6. Detects Defects in Complex Geometries
RT is effective for inspecting components with irregular shapes and hidden cavities.
Limitations of Radiographic Testing (RT)
Radiation Safety Concerns: RT involves hazardous ionizing radiation, requiring strict safety measures and regulatory compliance.
High Cost: The equipment, materials, and qualified personnel required for RT make it more expensive than some other NDT methods.
Time-Consuming: Traditional film processing can take time, though digital radiography (DR) and computed radiography (CR) reduce processing delays.
Limited to Certain Materials: RT is less effective for materials with low radiation absorption properties, such as thin plastics and some composite materials.
Applications of Radiographic Testing (RT)
1. Oil & Gas Industry
Inspection of pipelines and pressure vessels to detect weld defects and corrosion.
Evaluation of storage tanks and refinery components.
Ensures compliance with industry standards such as API 1104, ASME BPVC, and ISO 17636.
2. Aerospace Industry
Inspection of aircraft components, including engine parts, wings, and fuselage sections.
Detection of fatigue cracks, porosity, and bonding issues in composites.
Quality control of additive-manufactured (3D-printed) aerospace parts.
3. Power Generation
Inspection of boilers, turbines, and nuclear reactor components.
Evaluation of weld integrity in high-pressure systems.
Detection of corrosion in steam pipes and heat exchangers.
4. Marine & Offshore Industry
Structural assessment of ship hulls, offshore platforms, and subsea pipelines.
Corrosion monitoring of marine structures exposed to seawater.
Inspection of critical welds in oil rigs and shipbuilding.
5. Heavy Engineering & Manufacturing
Quality control of castings, forgings, and machined parts.
Detection of shrinkage cavities, cracks, and inclusions in metal components.
Ensures compliance with manufacturing standards like ASTM E1742 and ISO 17636.
Comparison of Radiographic Testing (RT) with Other NDT Methods
NDT Method Defect Detection Material Thickness Portability Cost
Radiographic Testing (RT) Internal defects Medium to thick Moderate High
Ultrasonic Testing (UT) Internal defects Medium to thick High Moderate
Magnetic Particle Testing (MT) Surface/subsurface defects Thin to medium High Low
Liquid Penetrant Testing (PT) Surface defects Thin High Low
Eddy Current Testing (ET) Surface/subsurface defects Thin to medium High Moderate
Conclusion
Radiographic Testing (RT) is a powerful and reliable NDT method that enables accurate detection of internal defects in materials and welded structures. Despite its safety concerns and high costs, its ability to produce detailed, high-resolution images makes it indispensable for quality control and safety assessments in industries such as oil & gas, aerospace, marine, power generation, and manufacturing.
At NDT AND PWHT SOLUTIONS PVT LTD (India), we provide advanced RT services using cutting-edge radiographic technology to ensure the highest inspection standards. Our team of certified radiographers follows strict safety protocols and industry standards to deliver precise, efficient, and reliable testing solutions.
Contact us today to learn more about our Radiographic Testing services and how we can help enhance the safety and reliability of your critical components.