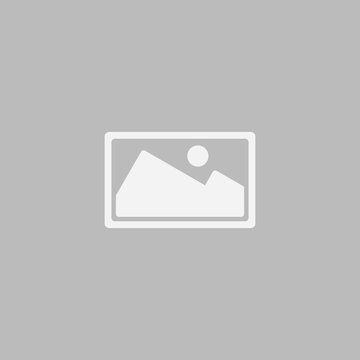
NDT for Oil & Gas: Pipeline and Pressure Vessel Inspections
Introduction
In the oil and gas industry, pipeline and pressure vessel integrity are critical to ensuring the safe and efficient transport of hydrocarbons and other gases. Non-Destructive Testing (NDT) methods play a pivotal role in detecting potential failures, ensuring that pipelines and pressure vessels are operating safely and efficiently.
At NDT AND PWHT SOLUTIONS PVT LTD (India), we provide state-of-the-art NDT services tailored to meet the demanding requirements of the oil and gas sector. This article explores the importance of NDT in pipeline and pressure vessel inspections and highlights the most effective NDT methods used in these applications.
The Importance of Pipeline and Pressure Vessel Inspections
Pipelines and pressure vessels are subjected to extreme conditions, including high pressures, corrosive environments, and mechanical stress. Over time, these factors can lead to the formation of cracks, corrosion, or other defects that, if left undetected, could result in catastrophic failures. Regular inspections are essential to identify these issues early and prevent costly repairs or dangerous incidents.
The main goals of NDT in pipeline and pressure vessel inspections are to:
Detect early signs of degradation, such as cracks, corrosion, or weld defects
Prevent unplanned shutdowns and service interruptions
Extend the operational life of critical infrastructure
Ensure compliance with industry regulations and safety standards
Common NDT Methods Used for Pipeline and Pressure Vessel Inspections
1. Ultrasonic Testing (UT)
Ultrasonic Testing (UT) is one of the most widely used methods for inspecting pipelines and pressure vessels. UT uses high-frequency sound waves to detect internal and surface flaws. The method is especially useful for:
Measuring wall thickness in pipelines and pressure vessels
Detecting corrosion, pitting, and cracks in metal components
Assessing weld quality and integrity
Modern Phased Array Ultrasonic Testing (PAUT) offers enhanced capabilities, allowing for faster and more accurate inspections of complex geometries and welds.
2. Radiographic Testing (RT)
Radiographic Testing (RT) involves the use of X-rays or gamma rays to create images of the internal structure of a material. RT is particularly effective for:
Detecting internal defects such as cracks, voids, and weld flaws
Examining welds and joints in pipelines and pressure vessels
Assessing the overall structural integrity of metal components
RT is a non-intrusive and highly detailed inspection method, making it ideal for evaluating critical components in pipelines and pressure vessels.
3. Magnetic Particle Testing (MPT)
Magnetic Particle Testing (MPT) is used for detecting surface and near-surface defects in ferromagnetic materials. It is often applied to:
Inspect welds and joints for surface cracks
Detect corrosion or wear on the outer surface of pipelines
Identify fatigue cracks in pressure vessel components
MPT is a fast and effective way to detect surface flaws in metal components, ensuring their reliability in the long term.
4. Liquid Penetrant Testing (LPT)
Liquid Penetrant Testing (LPT) is a surface inspection method that uses a liquid dye to highlight surface cracks, pores, and other defects. It is commonly used for:
Inspecting welds, joints, and pipeline surfaces
Detecting fine cracks and leaks in pressure vessels
Identifying defects in non-porous materials
LPT is a low-cost and straightforward method for detecting surface defects, providing rapid results for critical inspections.
5. Eddy Current Testing (ECT)
Eddy Current Testing (ECT) is a method that uses electromagnetic induction to detect surface and near-surface defects in conductive materials. It is particularly effective for:
Inspecting corrosion, wear, and cracks on pipe surfaces
Evaluating thin-walled components in pressure vessels
Detecting pitting and surface oxidation
ECT is highly sensitive to small surface cracks and is often used for targeted inspections of high-risk areas in pipelines and pressure vessels.
Advantages of NDT in Oil & Gas Pipeline and Pressure Vessel Inspections
Early Detection of Defects: NDT allows for the identification of cracks, corrosion, and other defects before they escalate into larger issues, potentially avoiding expensive repairs or catastrophic failures.
Safety Assurance: Regular NDT inspections ensure the safety of employees, contractors, and the surrounding environment by identifying and mitigating potential hazards in pipeline and pressure vessel systems.
Cost Efficiency: NDT methods are cost-effective compared to traditional methods of inspection or repair. By identifying issues early, companies can avoid costly downtimes and ensure continued operational efficiency.
Minimized Downtime: NDT methods, particularly automated and robotic systems, enable real-time inspections, reducing the need for shutdowns and minimizing the disruption of daily operations.
Conclusion
Non-Destructive Testing is an indispensable tool for ensuring the safety, efficiency, and longevity of pipelines and pressure vessels in the oil and gas industry. At NDT AND PWHT SOLUTIONS PVT LTD (India), we specialize in providing advanced NDT services that help our clients in the oil and gas sector maintain the highest standards of safety and reliability.
Our expert team uses a combination of the latest NDT technologies, including Ultrasonic Testing (UT), Radiographic Testing (RT), Magnetic Particle Testing (MPT), Liquid Penetrant Testing (LPT), and Eddy Current Testing (ECT), to deliver precise and reliable inspection results. By employing the most advanced inspection techniques, we ensure that critical pipeline and pressure vessel systems remain operational, safe, and compliant with industry regulations.