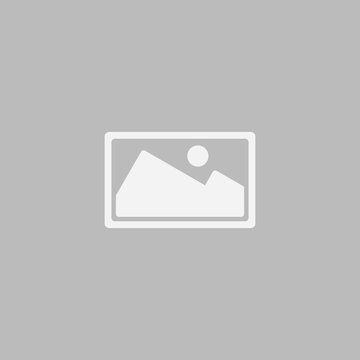
Ensuring Pipeline Integrity: Best NDT Practices for Oil & Gas Pipelines
Introduction
Oil & gas pipelines are critical infrastructure that require continuous monitoring and inspection to prevent leaks, failures, and environmental hazards. Non-Destructive Testing (NDT) plays a vital role in ensuring pipeline integrity, extending asset life, and maintaining compliance with international safety standards.
At NDT AND PWHT SOLUTIONS PVT LTD (India), we implement advanced NDT techniques to detect corrosion, cracks, and other pipeline defects before they become catastrophic. This article explores the best NDT practices used to safeguard pipeline systems.
Common Pipeline Defects and Their Causes
– Corrosion: Internal and external corrosion due to exposure to chemicals and environmental factors
– Cracks & Fractures: Caused by mechanical stress, fatigue, or defective welding
– Wall Thickness Loss: Due to erosion, corrosion, or aging materials
– Leaks & Structural Weaknesses: Resulting from pressure fluctuations or impact damage
Best NDT Methods for Pipeline Inspection
1.Ultrasonic Testing (UT) & Phased Array Ultrasonic Testing (PAUT)
– Detects: Thickness loss, corrosion, and cracks
– Advantage: High accuracy and ability to inspect through coatings
2.Radiographic Testing (RT) – Digital Radiography (DR)
– Detects: Internal defects in welds and wall thickness variations
– Advantage: Produces high-resolution digital images with real-time analysis
3.Magnetic Particle Testing (MPT)
– Detects: Surface and near-surface cracks in ferromagnetic pipelines
– Advantage: Quick and cost-effective for weld inspections
4.Eddy Current Testing (ECT) & Pulsed Eddy Current (PEC)
– Detects: Surface and subsurface defects in metallic pipelines
– Advantage: Ideal for detecting corrosion under insulation (CUI)
5.Time of Flight Diffraction (TOFD)
– Detects: Precise flaw sizing in welds and seams
– Advantage: Highly reliable for detecting hidden cracks
6.In-Line Inspection (ILI) with Smart Pigs
– Detects: Internal pipeline anomalies using electromagnetic and ultrasonic sensors
– Advantage: Allows long-distance inspection without disrupting operations
Advanced Technologies in Pipeline NDT
1.AI-Powered Defect Analysis
– Automated defect recognition (ADR) minimizes human error
– Machine learning models improve defect characterization
2.Drone-Based Pipeline Inspection
– Enables aerial thermal imaging for leak detection
– Inspects hard-to-reach areas with high-resolution cameras
3.Remote Monitoring & Cloud-Based NDT Data
– Real-time data access for global teams
– Improves traceability and regulatory compliance
Regulatory Compliance & Industry Standards
– API 570 & API 653: Pipeline and storage tank inspections
– ASME B31.8: Gas transmission and distribution pipelines
– ISO 17025 & ISO 9712: NDT certification and laboratory accreditation
Conclusion
Ensuring pipeline integrity is crucial for safety, environmental protection, and operational efficiency. At NDT AND PWHT SOLUTIONS PVT LTD (India), we deploy the latest NDT techniques, AI-driven analysis, and advanced inspection tools to help oil & gas companies maintain their pipelines with confidence.
By adopting these best practices, industries can prevent costly failures, extend asset life, and comply with global standards. Contact us today for expert pipeline inspection solutions tailored to your needs!