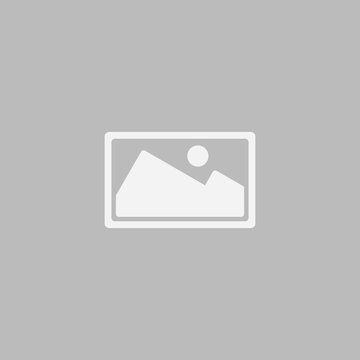
Eddy Current Testing (ECT) for Crack Detection in Metals
Introduction
Eddy Current Testing (ECT) is a widely used Non-Destructive Testing (NDT) method that employs electromagnetic induction to detect cracks and defects in conductive materials. It is particularly effective for inspecting metals and is highly valued for its sensitivity, speed, and versatility in detecting surface and near-surface flaws. At NDT AND PWHT SOLUTIONS PVT LTD (India), we employ advanced ECT methods to ensure the reliability and safety of critical components across various industries.
Principles of Eddy Current Testing
ECT works on the principle of electromagnetic induction, where a probe carrying an alternating current generates an eddy current in the test material. These currents create magnetic fields that interact with material defects, resulting in changes in impedance, which are then detected and analyzed.
The primary advantages of ECT include:
– High sensitivity to cracks, especially near the surface.
– Ability to detect both surface and subsurface flaws without the need for direct contact.
– Speed and portability, making it ideal for field inspections.
– No requirement for a coupling medium (such as gel or liquid).
How Eddy Current Testing Works
Probe Application – An alternating current is passed through a probe coil, which generates an electromagnetic field in the test material.
Current Interaction with Material – The induced current produces a magnetic field that interacts with defects (such as cracks, voids, or inclusions) within the material.
Defect Detection – The change in impedance caused by defects alters the flow of eddy currents, which is detected by the probe and displayed on a monitor for analysis.
Data Analysis – The impedance signals are analyzed to identify the type, location, and size of any defects.
Types of Eddy Current Testing
1.Surface Eddy Current Testing
– Used primarily for detecting surface cracks and corrosion.
– Ideal for inspecting thin materials, welds, and fasteners.
2.Eddy Current Array (ECA)
– Provides higher resolution and faster inspections by using multiple coils simultaneously.
– Ideal for large-area scanning and detecting multiple defects in a single pass.
3.Near-Surface Eddy Current Testing
– Effective for detecting subsurface cracks that are close to the surface, such as in heat-affected zones.
– Used in aerospace, automotive, and power generation industries for critical component inspections.
4.High-Frequency Eddy Current Testing
– Works well for detecting very fine cracks and surface defects in thin-walled components.
– Typically used for inspecting aircraft wings, fuselages, and pressure vessels.
Applications of Eddy Current Testing
ECT is applied in a wide range of industries to ensure the safety and integrity of critical components:
1.Aerospace
– Detects cracks in aircraft wings, fuselages, and engine components.
– Used for inspecting aluminum and composite materials.
2.Oil & Gas
– Ensures the integrity of pipelines, pressure vessels, and welds.
– Detects corrosion and fatigue cracks in subsea structures.
3.Automotive
– Inspects critical automotive components such as engine blocks, brake rotors, and suspension systems.
4.Power Generation
– Used for inspecting turbine blades, generator components, and boiler tubes.
5.Manufacturing & Fabrication
– Quality control in welding, casting, and forming processes.
Advantages of Eddy Current Testing
– Non-contact method, ideal for delicate or thin materials.
– Rapid results, enabling quick decision-making and immediate corrective actions.
– High sensitivity, capable of detecting very fine cracks and defects.
– Portable and versatile, suitable for both field and laboratory inspections.
– No need for a coupling medium (unlike ultrasonic testing or liquid penetrant testing).
Limitations of Eddy Current Testing
– Only effective for conductive materials such as metals.
– Requires trained personnel for interpreting complex impedance signals.
– Limited penetration depth, making it unsuitable for deep subsurface flaws.
Conclusion
Eddy Current Testing (ECT) remains a highly effective and efficient NDT method for detecting cracks and defects in metallic materials. At NDT AND PWHT SOLUTIONS PVT LTD (India), we use advanced ECT technologies to ensure that critical components are thoroughly inspected and free from potentially hazardous defects. Our expertise in ECT provides our clients with the assurance that their assets meet the highest standards of safety and quality.
By combining cutting-edge technology and highly skilled professionals, we deliver fast, reliable, and accurate defect detection solutions for a variety of industries.