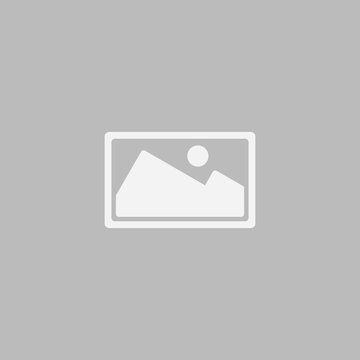
Cost Savings Achieved Through Predictive Maintenance with NDT
Introduction
In industries where equipment reliability is crucial, Non-Destructive Testing (NDT) plays a significant role in predictive maintenance, reducing downtime and minimizing costs. By utilizing advanced inspection techniques, companies can identify potential failures before they escalate into costly repairs or catastrophic failures.
At NDT AND PWHT SOLUTIONS PVT LTD (India), we specialize in NDT-driven predictive maintenance, helping industries optimize their maintenance schedules, reduce operational expenses, and improve asset longevity.
Understanding Predictive Maintenance with NDT
Predictive maintenance leverages real-time condition monitoring and historical data analysis to forecast equipment failures before they occur. By integrating NDT techniques into predictive maintenance strategies, industries can:
– Detect defects early, preventing unexpected breakdowns
– Reduce unnecessary maintenance and repair costs
– Extend the life cycle of critical components
– Improve safety and reliability
– Optimize resource allocation for maintenance teams
Key NDT Techniques in Predictive Maintenance
1.Ultrasonic Testing (UT) for Thickness Measurement
– Identifies wall thinning and corrosion in pipelines, pressure vessels, and heat exchangers.
– Helps in planning proactive maintenance schedules.
2.Infrared Thermography (IRT) for Heat Monitoring
– Detects thermal anomalies in electrical systems and rotating machinery.
– Prevents overheating-related failures in industrial equipment.
3.Eddy Current Testing (ECT) for Surface and Subsurface Defects
– Useful in detecting cracks, corrosion, and conductivity variations in metallic structures.
– Widely applied in power plants, aerospace, and oil & gas sectors.
4.Vibration Analysis for Rotating Equipment
– Identifies misalignment, imbalance, and bearing defects in motors, pumps, and turbines.
– Enables early corrective actions to prevent machinery failure.
5.Acoustic Emission Testing (AET) for Structural Health Monitoring
– Monitors real-time stress-induced crack propagation in structures and pressure vessels.
– Enhances safety by detecting critical flaws at an early stage.
Financial Benefits of NDT in Predictive Maintenance
1.Reduction in Downtime
– Prevents unexpected shutdowns, ensuring continuous production.
– Minimizes revenue loss due to equipment failure.
2.Lower Repair and Replacement Costs
– Detecting defects early reduces expensive emergency repairs.
– Increases component lifespan, delaying costly replacements.
3.Optimized Maintenance Scheduling
– Avoids unnecessary maintenance activities, reducing labor and material costs.
– Focuses maintenance efforts on areas that truly require attention.
4.Enhanced Safety and Compliance
– Reduces risk of catastrophic failures, protecting employees and assets.
– Ensures compliance with industry safety regulations and standards.
Industries Benefiting from NDT-Based Predictive Maintenance
Oil & Gas
– Pipeline and pressure vessel monitoring to prevent leaks and failures.
Aerospace
– Aircraft component inspections to reduce in-flight risks and maintenance costs.
Power Generation
– Boiler and turbine monitoring to increase operational efficiency.
Manufacturing & Heavy Engineering
– Structural health assessments to improve production uptime.
Marine & Offshore
– Ship hull and offshore rig inspections to ensure longevity in harsh environments.
Conclusion
Predictive maintenance powered by NDT technologies is transforming industries by delivering cost savings, improved asset reliability, and enhanced safety. At NDT AND PWHT SOLUTIONS PVT LTD (India), we leverage state-of-the-art NDT inspection methods to help businesses optimize their maintenance strategies, reduce operational costs, and extend the lifespan of critical assets.
By investing in NDT-driven predictive maintenance, companies can achieve maximum efficiency, minimized risks, and substantial cost reductions, ensuring long-term success in competitive industrial environments.