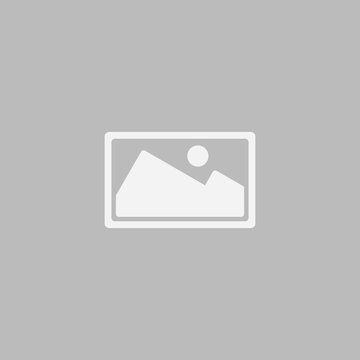
Comparison of Destructive and Non-Destructive Testing Methods
Introduction
Testing is an integral part of quality assurance in manufacturing and infrastructure maintenance. While destructive testing (DT) and non-destructive testing (NDT) are both employed to evaluate materials, components, and structures, they differ in their approaches and applications. Understanding the differences between these two testing methods helps industries choose the appropriate technique based on their specific needs.
At NDT AND PWHT SOLUTIONS PVT LTD (India), we offer comprehensive NDT services that allow industries to detect defects and ensure the quality and safety of their components without causing any damage.
Destructive Testing (DT)
Destructive testing involves the testing of materials or components to failure in order to understand their behavior under stress. This method is typically used for research and development, as well as for certification purposes.
Common Destructive Testing Methods
Tensile Testing: Measures the material’s strength and elongation until failure.
Impact Testing: Determines the material’s toughness by measuring its response to a sudden force.
Bend Testing: Used to assess ductility and strength by applying a force until the material bends or fractures.
Advantages of Destructive Testing
Provides data on material properties at the point of failure.
Ideal for new materials or when design specifications need validation.
Can be used for obtaining material fatigue limits and other critical information.
Disadvantages of Destructive Testing
Irreversible: The component being tested is destroyed, meaning it cannot be reused.
Higher costs: Due to the need for new or spare components and equipment for repeated testing.
Time-consuming: Multiple tests are often needed to gain meaningful data.
Non-Destructive Testing (NDT)
Non-Destructive Testing (NDT) refers to a set of testing methods that evaluate the properties of a material or structure without causing any damage. NDT allows for the detection of defects, corrosion, or structural weaknesses without affecting the part’s usability.
Common Non-Destructive Testing Methods
Ultrasonic Testing (UT): Uses high-frequency sound waves to detect internal flaws or measure thickness.
Radiographic Testing (RT): Uses X-rays or gamma rays to inspect the internal structure of components.
Magnetic Particle Testing (MPT): Detects surface and near-surface defects in ferromagnetic materials.
Eddy Current Testing (ECT): Uses electromagnetic induction to detect surface and near-surface defects.
Visual Testing (VT): The simplest form of NDT involving visual inspection of components.
Advantages of Non-Destructive Testing
No damage to components: The component remains intact after testing and can continue to be used.
Cost-effective: Compared to destructive testing, NDT is generally more affordable and can reduce material waste.
Time-saving: Provides real-time results, reducing inspection time and downtime.
Wide application: NDT can be applied to a variety of materials and industries without compromising the item being tested.
Disadvantages of Non-Destructive Testing
Limited in detecting certain types of defects (e.g., deep internal flaws in some materials).
Requires skilled technicians to interpret results accurately.
Some NDT methods may have limitations in certain material types.
Conclusion
While both destructive and non-destructive testing methods have their place in the industry, NDT offers clear advantages for most applications where component integrity and reliability must be assessed without sacrificing usability. NDT AND PWHT SOLUTIONS PVT LTD (India) specializes in providing advanced NDT services that help companies ensure the highest standards of safety, quality, and efficiency.
Choosing between destructive and non-destructive testing depends on the specific goals of an inspection. For most industries, NDT provides an efficient, cost-effective, and safe solution for ensuring long-term quality control.
Contact us today for more information on how NDT can benefit your industry and help maintain the safety and reliability of your assets.