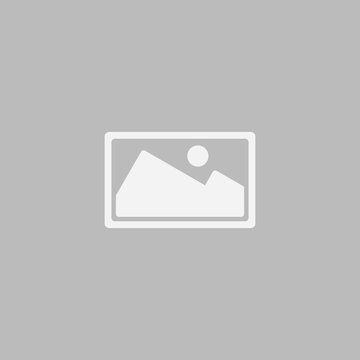
Aerospace Safety: The Role of NDT in Aircraft Component Reliability
Introduction
Aircraft safety and reliability are paramount in the aerospace industry, where even the smallest defect can lead to catastrophic failures. Non-Destructive Testing (NDT) plays a crucial role in ensuring the integrity of aircraft components by detecting flaws before they compromise safety and performance.
At NDT AND PWHT SOLUTIONS PVT LTD (India), we provide advanced NDT solutions to the aerospace sector, helping ensure compliance with international safety standards and extending the life of critical aircraft components.
Importance of NDT in Aerospace Safety
– Prevention of In-Flight Failures: Early detection of cracks, corrosion, and material fatigue
– Compliance with Aviation Regulations: Meeting standards set by FAA, EASA, and AS9100
– Cost-Effective Maintenance: Reduces the need for expensive part replacements
– Extending Component Lifespan: Enhancing durability and reliability
Key NDT Techniques for Aircraft Inspection
1.Ultrasonic Testing (UT) & Phased Array Ultrasonic Testing (PAUT)
– Applications: Detects internal defects in fuselage, wings, and engine parts
– Advantages: Provides precise imaging for weld and bond integrity assessments
2.Radiographic Testing (RT) – Digital Radiography (DR)
– Applications: Inspection of composite materials, turbine blades, and structural components
– Advantages: High-resolution digital imaging for defect analysis
3.Eddy Current Testing (ECT) & Alternating Current Field Measurement (ACFM)
– Applications: Detection of surface and sub-surface cracks in conductive materials
– Advantages: Ideal for inspecting fasteners, landing gears, and wing structures
4.Magnetic Particle Testing (MPT) & Dye Penetrant Testing (DPT)
– Applications: Locates surface defects in ferrous and non-ferrous materials
– Advantages: Quick, cost-effective, and suitable for small, intricate parts
4.Thermographic Testing (Infrared Thermography – IRT)
– Applications: Identifies hidden delaminations and heat damage in composite structures
– Advantages: Non-contact method with real-time imaging capabilities
5.Remote Visual Inspection (RVI) with Drones & Borescopes
– Applications: Internal and external inspection of hard-to-reach aircraft areas
– Advantages: Reduces manual labor and increases inspection efficiency.
Advanced NDT Technologies for Aerospace
1.AI-Powered Defect Detection & Predictive Maintenance
– Utilizes machine learning algorithms to detect anomalies faster
– Predicts component failure before it occurs
2.Automated NDT Systems & Robotics
– Used for high-speed, high-precision aircraft inspections
– Reduces human error and improves accuracy
3.Laser Shearography & Digital Holography
– Detects material inconsistencies in composite structures
– Non-contact method for high-sensitivity defect analysis
Compliance with Aerospace Standards
– FAA (Federal Aviation Administration) – Aircraft safety regulations
– EASA (European Union Aviation Safety Agency) – Compliance for European aerospace
– AS9100 & NADCAP – Aerospace industry quality certification
– MIL-STD & ASTM Standards – Military and commercial aerospace requirements
Conclusion
NDT is an indispensable tool in aerospace safety, ensuring that aircraft components remain structurally sound and free of defects. At NDT AND PWHT SOLUTIONS PVT LTD (India), we deploy state-of-the-art NDT techniques, AI-driven predictive maintenance, and automated inspection solutions to support the aerospace industry’s stringent safety and quality requirements.
By leveraging cutting-edge NDT technologies, airlines and aircraft manufacturers can enhance operational safety, reduce maintenance costs, and comply with global aviation standards. Contact us today for expert aerospace NDT solutions!