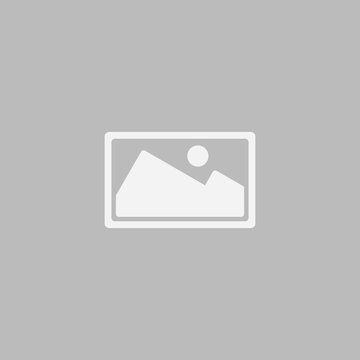
The Role of NDT in Marine and Offshore Inspections: Ship Hull and Structural Integrity.
Introduction
In the marine and offshore industries, the integrity of vessels and structures is of paramount importance. From commercial ships to offshore drilling rigs, these assets endure harsh environmental conditions, including saltwater corrosion, heavy waves, and extreme weather, all of which can accelerate wear and tear. Ensuring the safety and reliability of these structures is essential not only for operational efficiency but also for protecting human life and the environment.
Non-Destructive Testing (NDT) has become a critical part of marine and offshore inspections, providing an effective and non-invasive means of assessing the condition of ship hulls, offshore platforms, and other essential structures. This article explores the role of NDT in marine and offshore inspections, with a particular focus on ship hulls and structural integrity.
The Importance of NDT in Marine and Offshore Industries
Marine vessels and offshore platforms operate in one of the most demanding environments on earth. These structures are subjected to constant exposure to seawater, fluctuating temperatures, and mechanical forces from waves, winds, and cargo. Over time, this can lead to several forms of damage, including:
Corrosion: Seawater and humidity accelerate the corrosion of metal components.
Fatigue Cracking: Continuous mechanical stresses can lead to fatigue cracks in hulls, joints, and welds.
Erosion: The impact of water, debris, and ice can cause material erosion.
Weld and Structural Failures: The welding of components often results in weak spots that can fail under pressure.
Regular and thorough inspections using advanced NDT techniques are essential to detect these issues early and prevent catastrophic failures. By using NDT methods, marine operators and offshore engineers can ensure that their assets remain in good condition, prolonging their service life and preventing costly repairs or replacements.
NDT Methods Used in Marine and Offshore Inspections
1. Ultrasonic Testing (UT)
Ultrasonic Testing (UT) is widely used in the marine industry to inspect the thickness and integrity of metal components, particularly the hulls of ships and offshore platforms. UT uses high-frequency sound waves to detect internal defects such as cracks, voids, and material thinning. In marine inspections, UT is commonly used to:
Measure wall thickness of ship hulls and offshore platforms to detect corrosion or erosion.
Inspect weld joints for cracks, porosity, and other defects.
Assess material integrity in critical structural components, such as load-bearing beams and supports.
Advanced UT techniques, such as Phased Array Ultrasonic Testing (PAUT), offer detailed imaging and more accurate detection of flaws in complex geometries, allowing for comprehensive inspections of large and intricate areas.
2. Magnetic Particle Testing (MPT)
Magnetic Particle Testing (MPT) is particularly useful for detecting surface and near-surface cracks in ferromagnetic materials. This method is commonly used in the marine and offshore sectors for:
Inspecting ship hulls and offshore platforms for cracks, especially in critical areas such as joints, welds, and structural beams.
Identifying signs of fatigue in areas subject to heavy loads or mechanical stresses.
Examining welds and steel components for surface-breaking defects that could compromise structural integrity.
MPT is a rapid and effective method for detecting visible and near-surface flaws that could lead to failures if left undetected.
3. Eddy Current Testing (ECT)
Eddy Current Testing (ECT) is highly effective for detecting surface and near-surface defects in conductive materials. ECT is commonly used to inspect:
Ship hulls for surface cracks, pitting, and corrosion in areas that are difficult to inspect with other methods.
Offshore rig legs and supports for early signs of wear and erosion.
Marine structural components for material thinning, especially in high-stress areas subject to cyclic loading.
ECT is especially useful for inspecting non-ferrous materials, such as aluminum or copper alloys, which are commonly found in marine applications.
4. Radiographic Testing (RT)
Radiographic Testing (RT) uses X-rays or gamma rays to produce detailed images of the internal structure of materials. RT is particularly valuable for inspecting:
Welds and joints on ship hulls and offshore platforms, where defects such as porosity, inclusions, and cracks may be hidden from view.
Structural integrity of critical load-bearing components, such as beams and supports.
Internal corrosion and material degradation within steel components.
Digital Radiography (DR) offers enhanced image quality and faster processing times, making it an ideal solution for inspecting large areas quickly and efficiently.
5. Visual Testing (VT)
Visual Testing (VT) is the simplest and most commonly used NDT method for marine and offshore inspections. It involves visually inspecting components for visible damage, such as cracks, corrosion, or wear. VT is often the first step in any inspection process, helping inspectors identify areas that may require more advanced testing. VT is used to:
Inspect hulls, decks, and external structures for signs of damage or degradation.
Check for corrosion and other environmental damage in accessible areas.
Ensure proper maintenance of valves, pipes, and other components exposed to the elements.
While VT alone cannot detect internal defects, it serves as a crucial tool for identifying potential issues that require further investigation.
Benefits of NDT in Marine and Offshore Inspections
Safety Assurance: NDT ensures that ships and offshore platforms are free from structural defects, minimizing the risk of accidents, environmental disasters, or crew injuries.
Cost-Effective Maintenance: By detecting defects early, NDT allows operators to perform timely maintenance, preventing more extensive damage and reducing the need for expensive repairs or replacements.
Prolonged Asset Life: Regular NDT inspections help maintain the condition of ships and offshore platforms, extending their service life and improving the return on investment.
Environmental Protection: NDT prevents catastrophic failures that could result in oil spills, gas leaks, or other environmental hazards, ensuring that marine and offshore operations are conducted in an environmentally responsible manner.
Regulatory Compliance: NDT is essential for ensuring compliance with international safety and environmental standards, such as those set by the International Maritime Organization (IMO) and other regulatory bodies.
Conclusion
Non-Destructive Testing plays a vital role in ensuring the safety, reliability, and longevity of ships and offshore platforms. By using advanced NDT methods such as Ultrasonic Testing (UT), Magnetic Particle Testing (MPT), Eddy Current Testing (ECT), Radiographic Testing (RT), and Visual Testing (VT), operators can detect early signs of damage, corrosion, and fatigue, preventing costly failures and ensuring the continuous operation of marine and offshore assets.
At NDT AND PWHT SOLUTIONS PVT LTD (India), we specialize in providing state-of-the-art NDT services for the marine and offshore industries. Our expertise in NDT ensures that ships, rigs, and other offshore structures remain safe, operational, and compliant with industry standards. By leveraging advanced technology and our skilled inspection team, we help our clients safeguard their assets, improve operational efficiency, and protect the environment.