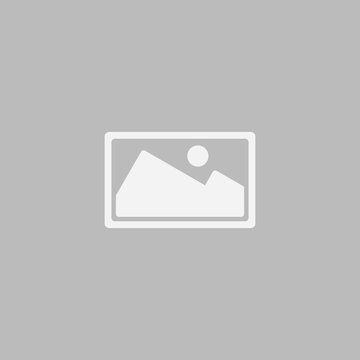
How to Choose the Right NDT Method for Your Industry
Introduction
Non-Destructive Testing (NDT) is an essential process used in various industries to ensure the safety, reliability, and longevity of components and structures. Choosing the right NDT method is crucial for obtaining accurate results and ensuring that inspections are effective, cost-efficient, and aligned with industry standards.
At NDT AND PWHT SOLUTIONS PVT LTD (India), we offer a wide range of NDT services tailored to the specific needs of industries such as aerospace, oil & gas, manufacturing, marine, and power generation. This article outlines the factors to consider when selecting the appropriate NDT method for your industry.
Factors to Consider When Choosing the Right NDT Method
1. Type of Material
The material being tested plays a crucial role in determining which NDT method to use. Different materials respond to various testing methods in different ways, and not all methods are suitable for all materials.
Metallic Materials (e.g., steel, aluminum): Methods such as Ultrasonic Testing (UT), Magnetic Particle Testing (MPT), and Eddy Current Testing (ECT) are effective for detecting cracks, corrosion, and surface defects.
Composite Materials (e.g., carbon fiber, fiberglass): Ultrasonic Testing (UT) and X-ray or Radiographic Testing (RT) are commonly used for assessing the integrity of composite materials, especially in aerospace applications.
Non-Metallic Materials (e.g., concrete, plastic): Visual Testing (VT), Ground Penetrating Radar (GPR), and Ultrasonic Testing (UT) are often used for non-metallic materials, depending on the inspection requirements.
2. Type of Defect to Be Detected
The type of defect you wish to detect significantly influences the choice of NDT method. Some methods are more effective at detecting surface defects, while others are better suited for subsurface or internal defects.
Surface Defects: Methods such as Magnetic Particle Testing (MPT) and Liquid Penetrant Testing (LPT) are ideal for detecting surface cracks, corrosion, and other surface anomalies.
Subsurface or Internal Defects: Ultrasonic Testing (UT), Radiographic Testing (RT), and Phased Array Ultrasonic Testing (PAUT) are excellent for identifying internal flaws, such as voids, cracks, and inclusions.
Fatigue Cracks: Eddy Current Testing (ECT) is commonly used for detecting fatigue cracks, especially in metal components.
3. Access to the Test Area
The accessibility of the area being tested plays a significant role in determining the best NDT method. Some methods require direct contact with the material or structure, while others can be performed remotely.
Hard-to-Reach Areas: For components located in hard-to-reach areas or dangerous environments, methods like Rope Access NDT, Remote Visual Inspection (RVI), and Ultrasonic Testing (UT) with robotic systems are ideal.
Large Structures: Large-scale structures, such as pipelines or offshore platforms, often require methods like Magnetic Particle Testing (MPT) or Radiographic Testing (RT) that provide comprehensive coverage of large areas.
Underwater Inspections: For submerged components, Underwater Ultrasonic Testing (UT) and Remote Visual Inspections (RVI) are commonly used.
4. Speed and Efficiency
The speed at which an NDT method provides results is often a key factor in determining its suitability. Some industries, such as oil & gas, require rapid inspections to minimize downtime.
High-Speed Inspections: Ultrasonic Testing (UT), especially with automated scanning systems, and Eddy Current Testing (ECT) are known for their quick data acquisition and real-time results.
Comprehensive Coverage: Methods like Phased Array Ultrasonic Testing (PAUT) allow for a fast and comprehensive assessment of large or complex components without the need for repositioning the probe.
5. Level of Detail Required
Different NDT methods offer varying levels of detail in terms of defect detection and characterization.
High-Resolution Imaging: For critical applications requiring detailed imaging, such as aerospace, Phased Array Ultrasonic Testing (PAUT) and Radiographic Testing (RT) provide high-resolution results for identifying small defects, cracks, or voids.
General Surface Inspection: For general surface inspection or preliminary checks, methods like Visual Testing (VT) and Magnetic Particle Testing (MPT) are often sufficient.
6. Regulatory and Industry Standards
Different industries and applications have specific regulatory standards and certifications that dictate the choice of NDT methods. For example:
Oil & Gas Industry: Standards such as API 510, API 570, and ASME Section V often require specific NDT methods like Ultrasonic Testing (UT) and Magnetic Particle Testing (MPT) to ensure the integrity of pipelines and pressure vessels.
Aerospace Industry: Aerospace components are usually tested with Radiographic Testing (RT), Ultrasonic Testing (UT), and Eddy Current Testing (ECT), based on the specific regulations outlined by bodies like FAA and ASTM.
7. Cost Considerations
The cost of an NDT method varies depending on the complexity of the technique, equipment, and the expertise required to interpret the results. Industries looking for cost-effective solutions may opt for simpler methods such as Visual Testing (VT) or Magnetic Particle Testing (MPT), while industries with higher safety and quality requirements may invest in more advanced methods like Phased Array Ultrasonic Testing (PAUT) or Radiographic Testing (RT).
Conclusion
Selecting the right NDT method for your industry is a critical decision that depends on several factors, including the type of material, the nature of the defect, access to the test area, the required level of detail, and compliance with industry standards. By understanding the advantages and limitations of each NDT method, you can ensure that the chosen method provides accurate, reliable results that meet your specific needs.
At NDT AND PWHT SOLUTIONS PVT LTD (India), we are dedicated to helping industries select the right NDT techniques to ensure the safety, quality, and efficiency of their operations. Our experienced team can assist you in determining the most appropriate NDT solution for your unique requirements, whether it involves routine inspections or complex assessments of critical components.
Contact us today to learn more about our wide range of NDT services and how we can support your industry’s needs.